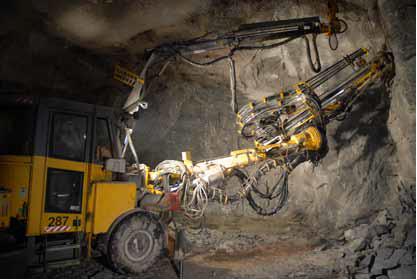
When the Diavik Diamond Mine went into production in January 2003, it had already achieved amazing feats of engineering. VP operations Marc Cameron tells Gay Sutton how the mine has rebounded from the 2008/2009 global financial crisis and is now completing a major investment to migrate from open pit to underground mining.
The Canadian diamond rush began in 1991 with the discovery of diamonds at Point Lake near Lac de Gras, opening a completely new chapter in Canadian mining. The region previously famed for its gold resources received a new lease of life, becoming the hunting ground for exploration companies large and small seeking these highly prized gems. Not only were Canadian diamonds of high quality, but the global marketplace was changing too, with a need for new sources of supply as established mines were reaching the twilight of their lives.
Today, the region around Lac de Gras supports three active diamond mines. The Diavik Diamond Mine, a joint venture between the global mining giant Rio Tinto and the international jeweler Harry Winston Diamond Corporation, lies on an island in the beautiful Lac de Gras almost 200 miles north east of Yellowknife, the capital of the Northwest Territories. The mine is run and operated by Diavik Diamond Mines Inc, a subsidiary of Rio Tinto. As neighbors, it counts the EKATI mine roughly 20 miles to the north, owned and operated by BHP Billiton, and the Snap Lake Mine some 70 miles to the south west, owned and operated by De Beers. Being only 140 miles south of the Arctic Circle, it’s true to say that almost everything that happens in Canada happens to the south of Diavik.
The climate at this latitude fluctuates between warm sunny summers and bitterly cold dark winters, and one aspect of life in this unique environment has been made famous the world over by the Ice Road Truckers TV series. The landscape between Yellowknife and the mines is one of innumerable lakes, where permanent roads could never be built. During the coldest months of the year, financed by a joint venture of the mines in the region, a massive effort gets under way to build an ice road over lakes that cover the landscape. The road runs some 375 miles starting at Tibbitt Lake and continuing past each of the operating mines. Inuit company Nuna Logistics begins construction in early January, then operates and maintains the road through its two month lifespan.
“The winter road usually opens in early February and is built to take light loads at first, progressing to heavy loads by mid-March and then generally closing in early April,” says Cameron. “During that two month period we bring in the entire year’s supplies of fuel, explosives and cement for the backfill in our underground operation.” Any new equipment or replacement parts that are required at the mine are also hauled in on the winter road. Purchases are generally made the previous summer so they can be manufactured and shipped to Edmonton in time for the long haul to Yellowknife and onto the winter road. Last year some 120,000 tonnes of materials and production equipment moved along the winter road, 40,000 tonnes of which were destined for Diavik.
“Perhaps one of the greatest challenges we have experienced in our operations was the very warm winter of 2006,” says Cameron. “The winter road’s operating window shrank from around 60 days to just 28, with a significant portion of that only being for light loads. We brought in some of the biggest helicopters and cargo planes in the world from Russia to operate an extensive airfreight program that lasted almost eight months.” The program was logistically very complex and came at an enormous cost, exceeding $30 million. “But it enabled us to continue operating throughout the year.”
The mine itself is also a triumph of engineering. The three kimberlite ore bodies are not on dry land but are located below the waterline on the lakebed, and two highly engineered dikes designed to function efficiently under all weather conditions hold back the lake’s massive weight of water and ice. The larger of the two pits, the A154, contains the north and south kimberlite pipes and has been in production since January 2003, while the smaller of the two, the A418, went into production in 2007.
The original mine plan proposed that once the two open pit mines reached their maximum working depths, underground mining would commence, following the kimberlite pipes downwards and extending the life of the mine to the planned 16 to 22 years. In accordance with that plan, the company initiated an $800 million dollar construction program in 2005 to prepare for the change. This included constructing approximately 13 miles of tunnels connecting to each of the pipes, along with all the usual facilities such as rescue bays, washrooms, ventilation, pumps and storage areas. On the surface a new crusher and paste backfill plant were added, and expansions were made to many existing elements of infrastructure such as water treatment and power plants, accommodation and mine buildings.
The plan was to wind down open pit mining on the A154 pit and begin mining the north and south kimberlites from underground in 2008, and then do the same for the smaller A418 pit by 2010.
When the global financial crisis broke in 2008 construction of the underground mine works was well advanced, and some 50 percent of the capital funding had been spent. Then sales fell through the floor. “The market for diamonds, especially in the US, deteriorated and for us it was a matter of survival, although we didn’t like to use that word at first,” Cameron says.
Acting quickly, the company developed a plan of action to protect the mine’s future. The first move was to reduce output by 50 percent, followed by the decision to shut down diamond production completely for a six week period. All underground expansion work was put on hold. It was a time of great uncertainty, and the company took a number of steps to protect its workforce, and reduce their understandable anxiety.
“We engaged with the workforce and were very open in letting them know exactly where the business stood. And to lessen the impact of the closure on the workforce we introduced various human resources programs, such as combining personal leave and holidays during the shut-down period,” Cameron says. “Looking back on it now, I think this approach brought us together as a company and helped us through this difficult period.”
The diamond industry showed considerable resilience and had picked up again by early 2010. “But it wasn’t until mid-2010 that I began to feel that the workforce had regained confidence and were returning to the normal heartbeat of operational mine efficiency.” Today, sales are very healthy and have overtaken those of the pre-crisis period.
With the finances back on track, work resumed on the underground expansion and is forging ahead. Underground mining commenced in the larger of the two pits in February 2010, and the smaller open pit will follow suit in mid-2012.
Underground mining has brought about significant changes, and Diavik has been working closely with its staff to ease the transfer to completely new methods of mining. “Over the last two years we have been running a very successful program referred to as the My Future Plan,” says Cameron. “We’ve been working with every employee whose job was likely to be affected by the closure of the open pit, identifying who would like to continue working at Diavik and what type of job they would like to do.”
Many have been put through a training program to develop their competencies in underground mining while others have moved into the company’s apprenticeship program. And the scheme has been a great success. Of the 160+ people employed at Diavik’s open pit operations, over 110 of those have moved to jobs elsewhere in the business, the majority of them transferring underground.
The company is currently in the process of expanding its apprenticeship scheme to underpin its future in a region where skills are in seriously short supply. Over the past eight years some 30 northerners have completed the Diavik apprenticeship program achieving journeyperson certifications. There are 25 people in the scheme this year alone, and the aim is to train at least 90 more people in trades such as instrumentation, mechanical and electrical engineering over the next 10 years.
Learning, however, is not something that is applied to the workforce alone. Through all Rio Tinto operations, experiences are shared, and learning events inform and improve operational processes. Safety is an obvious example of this. The Diavik safety management processes are rigorous, based on those developed by Rio Tinto over the past 60 years, and regularly audited by the parent company to ensure standards aren’t slipping. “We have multiple layers of safety programs,” says Cameron. “Many of the Rio Tinto processes are adapted to our mine conditions, and we’ve also implemented programs that other business units don’t have. We pay a hefty premium for this, but in everything we do, it’s to prevent a fatality or major disabling injury, and we are always learning.” Diavik’s safety efforts are being noticed. In fact, the mine’s workforce has won five John T. Ryan safety awards –Canada’s most prestigious safety awards.
The job hazard assessment, for example, has evolved considerably over time. Originally it was a matter of talking through each step of a task to establish the hazards and existing accident prevention controls, and then to decide whether any further safety processes should be put in place. Realizing that things could be missed when this was performed away from the worksite, the “Take Five” program was launched. This walked through the jobsite to check the reality against the discussed assessment. Finally, the process evolved to include the written take five, where all staff carried booklets to write down changes as they happened or as they were identified so that nothing would be missed.
Another recent initiative is the safety blitz, where senior management regularly visit the mine areas and engage with the workforce to find out about any hazards that have been identified, and to reinforce the safety imperative.
The financial crisis and the two year break in mine development presented significant challenges, but much has also been learned from the experience. During the two years the project was on hold, millions of dollars of infrastructure and equipment had lain idle across the island. “A great deal of refurbishment was required for some of that equipment,” says Cameron, “and there were significant unknowns. There were other issues that surfaced too; some of the contractors had moved on, for example, and a great deal of knowledge had been lost.”
The entire episode has been a valuable learning experience for both Diavik and Rio Tinto. Not only will it inform the planning and management of any future shutdown processes, but it underlines the importance of a strong interface between mine planning, macro-economic factors and marketing strategy.
Looking to the future, exploration continues to be a priority and considerable work is going into analyzing the results of exploration work carried out over the last seven years. On average it takes around 10 years to develop a new mine, taking into account all the assessments and permitting ahead of construction. So the Diavik operations will soon be reaching a critical point. “We would like to find new sources of supply within the next few years,” Cameron said. “We’ve found some interesting results that we are taking a second look at.” He would not give any more away, but although nothing is certain in mining, there is much to look forward to at Diavik.
DOWNLOAD
Diavik_SEPT11_NA_BROCH_s.pdf