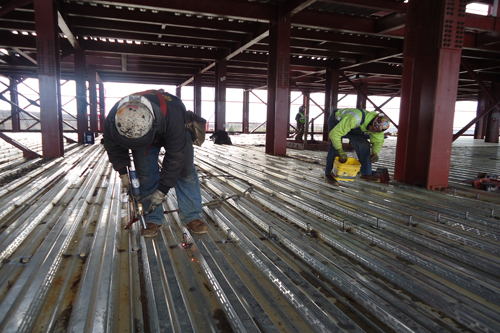
Discovered in 1866, the Mesabi Iron Range is the chief deposit of iron ore in the United States. Located in northeast Minnesota, within a jurisdiction which has long boasted a track record of successful mineral developments and operations, it is a vast deposit of the mineral that was extensively mined throughout the early part of the 20th Century through to the late 1960s, when natural ore reserves were depleted.
It was at this time that Butler Taconite, a company jointed owned by the Inland Steel Company, Wheeling-Pittsburgh Steel Corporation and Hanna Mining Company, developed a taconite mining operation at the site, which allowed it to commence operations in 1967, producing high-quality pellets until May 1985.
The closure of Butler Taconite resulted in the property being reclaimed and the plant dismantled. In September 1996, Minnesota Iron & Steel (MIS) was registered as a corporation with the goal of reopening the mine site and constructing a whole new facility, not only as an iron pellet producer but also as a direct reduced iron and electric arc furnace steelmaking facility.
It was in 2004, that the project was reactivated by Minnesota Steel Industries (MSI), a company formed by one of the major stakeholders of MIS. A feasibility study was prepared in 2007, and environmental permits were granted for a 4.1 million tonnes per annum pellet plant (MTPA), a 2.8 MTPA direct reduced iron facility and a 2.5 MTPA electric arc furnace. Subsequently, in October 2007, Essar Steel Holdings acquired the fully-permitted project from MSI.
Essar Steel Minnesota LLC (ESML), a wholly-owned subsidiary of Essar Resources Inc., can today be found building a state-of-the-art open pit mining, concentrating and pelletizing plant at the site. This undertaking began life as a greenfield pellet plant project in northern Minnesota, on the western end of the Biwabik Iron Formation, with a 19,000-acre project boundary, of which 4,360 acres are mineral lease land.
ESML has measured and indicated mineral resources of approximately 1,768 million metric tonnes of iron ore as well as inferred mineral resources of approximately 201 million metric tonnes of iron ore. Construction and development of the project commenced in October 2010, with ESML expecting operations to commence in the fourth quarter of 2014, ramping up to an annual production capacity of seven MTPA in quarter three of 2015.
All of the required Federal and State regulatory permits and approvals for the seven MTPA pelletizing capacity have been received, while permits and approvals for 1.8 MTPA of direct reduced iron (DRI) and 1.5 MTPA of electric arc furnace based steel are also in place. Project financing is fully committed for the commissioning of 4.1 MTPA pelletizing capacity, while obtaining additional project financing for the incremental 2.9 MTPA is in process.
ESML possesses the flexibility necessary to produce standard, fluxed and direct reduction grade pellets. The company’s aim is to be one of the lowest cost producers of said pellets in North America by utilising the ore body characteristics of its location area and the significant technological improvements that have occurred since the building of the last pellet plant in the US in the 1970s. Strategically located alongside multiple access points to a first class ground transportation infrastructure the company is perfectly placed to serve the North American market, while multiple vessel options in its vicinity give it access to the international seaborne market.
The nature, location and scope of the mine itself allows for less capital equipment to be employed in mining operations, a factor that is expected to result in significantly reduced operating costs over time. The short haulage distance from the mine to the coarse crusher also provides significant operational cost-savings. Ultimately the plant will feature a two-stage crushing circuit, which will increase mill throughput, as compared to a single mill operation. Moreover, transporting the slurry via pipeline will provide the ESML with substantial cost savings over rail and road transportation. The project site will also have a slurry storage capacity of 60,000 tonnes, which is intended to reduce process interruptions.
ESML carries with it a steadfast belief that through a combination of teamwork, training, communication and shared responsibility, it can maintain a workplace free of injury, illness or environmental incidents. Most importantly, the company ensures that it achieves continuous improvement in health, safety and environmental performance by creating a culture of employee ownership. To that end, it strives to involve employees at all levels of the organisation in the creation of policies and procedures and seek to ensure that any issues are resolved in a timely manner at the appropriate organisational level.
Before a company can develop and operate a mine in the state of Minnesota it must first complete an Environment Impact Statement or Study, before then obtaining the appropriate environmental permits and approvals which grant permission for the construction and operation of production facilities, as well as the final reclamation of the mine site.
Accordingly, ESML has obtained all of the necessary permits and approvals to increase pelletizing capacity to 7.0 MTPA. A supplemental Environmental Impact Statement for a 7.0 MTPA iron ore pellet plant was approved by the Minnesota Department of Natural Resources on December 29th, 2011 after undergoing a public review process. In addition the company obtained a Permit to Mine from the Minnesota Department of Natural Resources on April 17th, 2012 and an air permit from the Minnesota Pollution Control Agency on May 10th, 2012.
Furthermore, the company has engaged environmental consultants to evaluate the increased capacity envisioned in Phase II of the project. The environmental review and permitting process for the additional capacity will involve the preparation and submission of a further Environmental Impact Statement, as well as the amendment of all of the current environmental permits.
ESML realises it also has a responsibility to give back to the community that supports it in many ways. The company’s employees can regularly be found volunteering their time, and making financial contributions, towards various initiatives including local programmes United Way and Food Shelf, and towards local schools, universities and hospitals. In addition to these, ESML’s employee driven Community Connections Committee coordinates vital outreach efforts to several of the region’s leading non-profit organisations.
Written by Will Daynes, research by Peter Rowlston