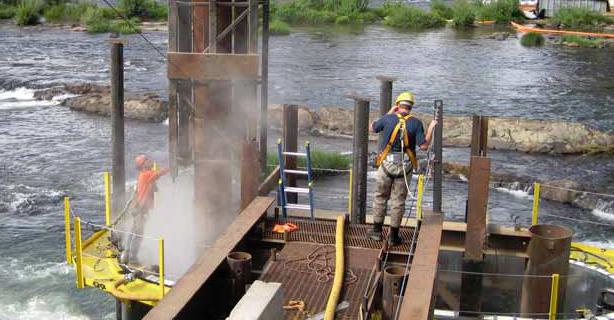
A large number of regulatory environmental agencies in Oregon get involved when you demolish one bridge and construct another, David Hendricks learns from Hamilton Construction’s Kevin Parrish.
Founded in Springfield, Oregon, in 1939, Hamilton Construction has grown from a small construction company building concrete roads and irrigation systems to a full-scale general contractor and AISC steel fabricator and erector specializing in bridges and railroad trestles in the US Northwest. Its portfolio includes projects in Alaska, Arizona, California, Colorado, Idaho, Montana, Nevada, Oregon, Utah, Washington and Wyoming.
Offering design-build services, the company has a mix of private- and public-sector clients, from the state transportation departments of Oregon, California and Washington to Weyerhaeuser, Georgia Pacific, Portland General Electric, Union Pacific Railroad and Burlington Northern Santa Fe Railway, as well as several short-line railroads. Heavy highway and bridge construction is the core of Hamilton’s work.
One of its current projects is close to Hamilton’s home base—the $187 million Willamette River Bridge that will replace a decommissioned bridge connecting the municipalities of Eugene and Springfield. Hamilton is providing construction management and general contractor (CMGC) services for this new arch deck design bridge project, replacing the existing temporary bridge built there in 2004, which replaced the original bridge (built in 1961) that was discovered to contain shear cracks. Hamilton’s project manager Kevin Parrish says that a major concern and challenge for building bridges in the Pacific Northwest is the Endangered Species Act.
“We in the construction business in this part of the world take measures to protect threatened and endangered wildlife, in this case the Chinook salmon in the Willamette River,” says Parrish. “Since this river is home to the Chinook, it’s considered critical habitat, so we have to do a number of specific things to avoid impacting the habitat or the fish. Another major issue in building bridges here is maintaining a sequence in carefully staging the project, to enable a constant flow of traffic—in this case two lanes in each direction, Interstate 5 being a heavily traveled route in the area. We also have to maintain a single lane of traffic in each direction on Franklin Boulevard [also known as SR 99], a surface street that travels under the interstate highway. Oregon is a green state, and we also have the demands of the surrounding environs of the Eugene and Springfield areas, with the interstate being a boundary between the two cities.”
Parrish explains that Springfield is “gritty and industrial” compared to Eugene, home to the University of Oregon, with its activist student body and surrounding community very involved in environmental issues, “with a heightened awareness of what is going on in their area.”
The first step in the staging process was demolishing the decommissioned bridge, and environmental permits specified that no materials be allowed to fall into the water. It required the construction of containment platforms—as well as coordination of demolition operations over Franklin Boulevard—and platforms over wetlands and sensitive areas between Franklin and the Union Pacific Railroad mainline tracks, which required railroad-approved containment platforms over the tracks. There were coordinated efforts to maintain traffic flow on surface streets, as well as rail traffic, with appropriate timelines for when flaggers would stop train traffic in order for the demolition crew to remove debris without endangering rail cars.
Obtaining permits for the various aspects of the project was a lengthy process in itself, Parrish says. Oregon has a special programmatic environmental permitting process that was developed in conjunction with the National Marine Fisheries Service (a division of the National Oceanic & Atmospheric Administration). Add to that the Army Corps of Engineers, the Bureau of Reclamation, the Oregon Department of Fish & Wildlife, the Oregon Department of Ecology, the Environmental Protection Agency and the Department of State Lands.
“Every regulatory agency involved with the environment is a party to these permits,” Parrish explains, “and the Oregon Department of Transportation [ODOT] implemented them because in 2002 they realized that since they had a number of bridges to replace, they needed a speedier way of permitting—I estimate that Hamilton has built at least one-quarter of the bridges in Oregon. So ODOT worked with these regulatory agencies to produce a list of conditions of environmental performance standards that, if met, would provide approvals without lengthy public reviews. There’s another process for developing design exceptions or permit variances. The issue of being granted a permit involves the work to be performed under the normal high-water line. All the information for the permit process had to be provided in sufficient detail that the regulatory agencies could determine what kind of work we’d be doing and how we were going to perform the work in compliance with the environmental performance standards in the programmatic permits.”
There’s another wrinkle: the Hydro Acoustic Noise Attenuation Program, which scientifically monitors the effects of the noise created by driving steel piles for bridges with a diesel (actually vegetable oil, usually canola or peanut oil) impact pile hammer on fish—or more specifically, on fish flotation bladders. It’s been found that in certain fish, the noise will cause bladders to vibrate, and in some species to burst. “The hydro-acoustic monitoring is a new program for Oregon,” says Parrish, “so it’s new for this bridge project, and the Willamette River is a shallow, fast-moving stream, with a substrate of pure bedrock. My concern was that when we drive steel piles into rock, it’s loud. We discovered that one of the best ways to attenuate the sound is by putting foam inside a steel pipe larger in diameter than the pile being driven, and then surrounding the pile with a curtain of air bubbles. The air bubbles are produced by pumping a huge volume of air through small orifices in pipes enclosing the piles. For our situation, since we have difficulty going very deep into the rock, we’ve developed templates and braces that hold the pile in place to support it. We had nearly 300 piles to drive.”
The work bridge and demolition containment structure under the existing demolition bridge was 850 feet long and 155 feet wide. Once the old bridge was removed, the next step was drilling the foundations for the southbound lanes of the new bridge; the drilling is now complete. “Slayden Construction Group of Stayton, Oregon, is our largest subcontractor; they’ve done CMGC work before,” says Parrish. “OBEC Consulting Engineers of Eugene and T.Y. Lin International of Salem provided engineering services. The key to this project was pre-planning. Everything had to be integrated; it’s not efficient to design a work bridge, then remove it, then design, build and remove a falsework system, then re-install the work bridge—because the timeline was critical for coordinating all the elements. We started working on the proposal early in 2008, and the bridge should be complete by the fall of 2013.”www.hamil.com