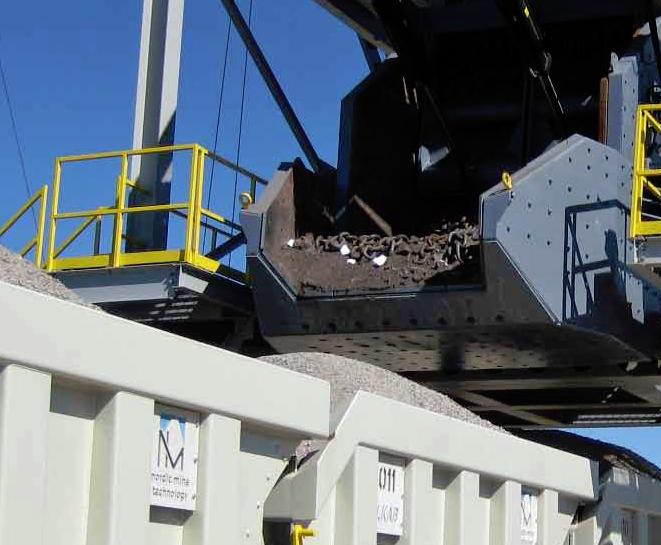
Nordic Mine Technology is pushing the boundaries in customised rail haulage systems for the mining sector. Philip Brown talks to Gay Sutton about innovation and growth.
When innovator and entrepreneur Eric Nylund formed Nordic Mine Technology (NMT) in 1987 and began to take his unique concept in rail haulage systems to the global mining industry, he was actually building on a programme of development that goes a lot further back. In 1968, while working as head of the design team for the Swedish mining and minerals company LKAB, Nylund had an idea that he developed into a completely new system for LKAB’s Kiruna iron ore mine in Sweden.
“The concept behind Nordic Mine Technology is continuous loading and unloading, and this markedly increases the efficiency of the overall operation,” explained NMT business development manager, Philip Brown. “In a typical rail haulage system, the train pulls up beneath the loading facility, the car is loaded and the train moves forward to allow the next car to be loaded, and so on. So it’s a one by one process of stop/start. And exactly the same happens for unloading. With our system, the train slows but does not stop during loading or unloading.” The increased efficiency of this system can enable mines to produce a higher tonnage of ore each day and of course the profits from this go straight to the bottom line.
After developing and proving this concept at the Kiruna mine, Nylund went to Canada to set up an LKAB office to market the new product to the rapidly expanding Canadian mining sector. But it wasn’t until Nylund acquired the rights to his designs and launched NMT in 1987 that he was able to take the new product worldwide. With engineering flare mixed with shrewd business acumen he won contracts to design and install his revolutionary system for a number of high profile companies as well as for many smaller ones.
Among the most prestigious projects that were completed during those early years was a rail system for BHP Billiton at the Olympic Dam—a massive copper, uranium and silver mine near Adelaide, Australia—and another for Ashanti Goldfields at the Obuasi mine in Ghana. And interestingly, Nylund also installed the first ever high-speed efficient tramming system in Russia.
Today, NMT is owned by Minesteel Fabricators of North Bay, Ontario, a company that for many years had been the licensed manufacturer for Nylund. There were many synergies between the two companies, with both being focused on quality. Minesteel dealt with the vertical movement of ore and Nordic with the horizontal movement. It therefore seemed a natural move that, on his semi retirement in 2006, Nylund should sell the company to his previous manufacturing partner.
Innovation continues to be a key element in Nordic’s success. The basic concept of continuous loading and unloading may have remained unchanged over the years, but the delivery of that concept has continuously developed. Today, the rail systems—which include the delivery chutes, dump stations and rail cars—are highly engineered and customised to meet the individual needs and characteristics of the mine. “One of the most common customisations we are asked to perform is to adapt the size and inclination of the chute to handle different types of ore, which can come in the form of large or small rocks and have various consistencies from wet and sticky to dusty and dry,” said Brown. “But we may also be asked to make allowances for wear, or to individually design the platforms for maintenance purposes.”
In addition to the increased efficiency of its products, the company has built its reputation on designing and delivering systems that are of high quality, very durable, and capable of running for many years with only the minimum of maintenance. All of this adds significantly to the value to the product. “We’re not the least expensive in the market,” said Brown, “but capital outlay is only one component of overall cost. We have some systems in place that have been running for more than 20 years requiring only typical consumable maintenance—things like replacing worn bearings and cylinders. Therefore, if a mine was to install a cheaper system that lasts just five to eight years, that system could potentially need replacing two or three times during the 20 year span of one of ours.”
Since becoming part of Minesteel, NMT has continued Nylund’s strategy of investing in R&D, adding new products and technologies to its portfolio, an example of which is the re-railing device, sold to its first customer in 2008. “Derailments can often happen underground. In the past you would have seen guys trying to put the cars back on the track by pure brute force. Our hydraulically operated re-railing device enables the cars to be lifted, levelled, and placed back on the track safely.”
There are a number of current products under development, but Brown was understandably loath to share the details. “The rail haulage industry is very competitive,” he said, “and it doesn’t take long for the knowledge to get around. Once we launch a new product we’re lucky if we have a year or two before our competitors are offering the same thing, so we tend to keep pretty tight lipped about it.”
The company has also been investing in new technology and facilities. One of the biggest investments over the past three years, and indeed one which has a significant impact on the engineering and procurement elements of the business, has been the introduction of 3D modelling. Costing around C$40,000 for software and C$50,000 for hardware, the modelling package also includes finite element analysis, and full motion analysis. “Our engineers can therefore run a ‘virtual’ train through the system, applying real-time gravity and so on, and can evaluate the advantages and disadvantages of a variety of engineering options,” he said. “That’s raised our engineering capability to a whole new level.
“We are also in the midst of a plant expansion,” he continued. “The expansion totals 1050m2 and will include increased manufacturing stations and crane capacity. In 2008 we constructed a 1 kilometer long rail haulage test track which includes provisions for loading and unloading of mine cars and trucks. This enables us to test our clients’ equipment prior to shipment, if so required, and also to test new technologies that we are developing.”
The current mining boom is presenting NMT with many opportunities. Just recently, the company won a major contract to design and test the rail system for the new expansion at the LKAB iron ore mine, a technically advanced installation and one of the most productive underground iron ore mines in the world. The new system, which includes six trains of 1200 tons and some 40 loading points, is scheduled to begin operating by the end of 2012.
Because of its location in North Bay, NMT is well placed to continue serving the needs of the flourishing North American mining sector, but Brown sees more potential growth elsewhere. “The Australians and Europeans, for example, have a different mindset and are very open to suggestions or to brainstorming new ideas,” he said, which fits very well with NMT’s focus on custom engineering and innovation. “So I think from the Nordic standpoint, the future is definitely in the export market.”