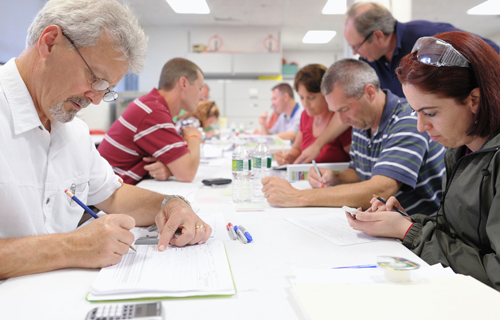
An approach to production practices that emphasises efficiency through the systematic identification and elimination of waste, the lean approach was derived from the Toyota Production System, developed in 1948. The lean approach seeks to produce the maximum amount of value for the customer from resources expended in production.
"Lean is about the endless pursuit of converting resources, materials, equipment, labour and energy most effectively and efficiently,” says Glenn Uminger, the University of Kentucky’s Lean Systems Program director. "The goal is to deliver the highest customer satisfaction with zero waste, while providing an engaging and rewarding environment for employees and delivering a good return for shareholders. This applies to any industry, including manufacturing, service, transportation, healthcare, restaurants, even government.”
This year marks 20 years since the University of Kentucky took its first steps towards becoming what is today recognised as being one of the world’s leading lean systems trainers.
Prior to 1994, no comprehensive academic study of the Toyota Manufacturing System had been conducted, nor did an academic centre exist where the principles of the system could be explored and taught, refined, elaborated, and tested experimentally. This all changed in March of that year when Fujio Cho, president of Toyota Motor Manufacturing U.S.A. in Georgetown, Kentucky, sent what would become a historic letter to Kozo Saito, professor of mechanical engineering at the University of Kentucky’s College of Engineering. The letter outlined the goals of a proposed collaboration between the University and Toyota, and marked the establishment of a partnership for research on painting technology and lean systems training that has flourished now for two decades.
Working with Toyota, the University of Kentucky’s College of Engineering established the Lean Systems Program to provide training in the Toyota Production System. Starting in 1996, the program began to offer certification in Lean Systems, currently featuring former Toyota employees as instructors. Leadership training was also first offered that year, with the creation of the Lean Executive Leadership Institute. A year later, in 1997, the University played host to the first International Lean Manufacturing conference, featuring a keynote address by Mikio Kitano, president of Toyota's Kentucky manufacturing operations, while in 1998, the Toyota Fellows Program was created to provide a unique opportunity for students who want to help shape the future of manufacturing.
During the course of the last 20 years the Lean Systems Program at the University of Kentucky has grown into a successful program. Through the Lean Certification Program, the Lean Executive Leadership Institute, and a variety of different custom-tailored training opportunities, an average of 1,500 attendees from about 75 different companies are served by the program each year.
“The Lean Systems Program has been truly fortunate to experience the benefit of Dr. Cho’s vision, and has developed and flourished,” Uminger said. “Overall we are humbled to be in a position to truly make a difference and contribute to society.”
Saito meanwhile believes that the program will continue to find ways to grow and improve. "When we started Toyota-sponsored lean and R&D programs, Toyota president Cho gave us his advice: ‘Do not rush, but keep in mind a steady gradual progress over many years to come.’ We’ve kept his advice in our hearts, but never thought we could reach our current status. The Lean Systems Program itself has served over 20,000 people from 48 states and 33 countries over 20 years. We couldn’t have accomplished that without practising continuous improvement. But we can’t stop here, and will continue our journey for the benefit of Kentuckians, the state, the nation, and the world.”
The 20th anniversary of the program will be formally observed of 28 October, 2014, with a special program jointly coordinated and sponsored by the University of Kentucky and Toyota. Held in conjunction with the Fourth Annual Lean Users Conference, the celebration will include a reception and dinner with special speakers, company displays and a video, and will be covered in greater depth within Business Excellence later in the year.
Written by Will Daynes, research by Vincent Kielty