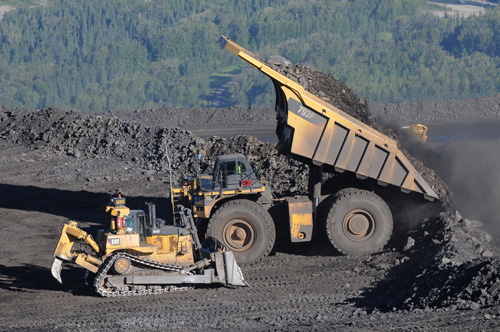
As reported last year, just a year in from its $3.3 billion purchase of Western Coal, Walter Energy had succeeded in dramatically increasing the output of the three Canadian mines. Wolverine, Willow Creek and Brule located near the towns of Tumbler Ridge and Chetwynd have all seen further rationalisation and improvement in the intervening year. Dan Cartwright, president of Walter Energy’s Canadian operations, though his brow may be knitted over global coal prices and a market over which he can have little influence, has plenty to be pleased about.
Let’s start with the big one. Some really significant improvements in safety have been achieved over the last twelve months. “We have seen a rapid drop in the rate of reportable incidents at all three of our operations,” says Cartwright. “At the Wolverine mine for example, in September we celebrated a full year without a lost-time incident (LTI) for the first time in the facility’s history.” At the newer Brule mine too, a year has nearly passed with no reportable incidents at all, something that rarely happens in the endemically hazardous coal mining industry. “We are particularly proud of the Brule team and the results they have achieved,” he adds.
These things don’t happen by luck – it takes the efforts of the entire team, he stresses. The approach of Walter Energy is to breakdown every activity and analyse it step by step. Safe Job Procedures have been developed for the majority of tasks within the Company. You can’t hope to finish this process because jobs change and new jobs arise: this is part of a culture of continuous improvement that by definition is never-ending.
Nevertheless the process has had a great bearing on the success achieved. “We have established a safety contact policy that requires each supervisor to make a certain number of safety contacts each week.” This involves observing the person at work then taking time with them to compliment work done well, challenge where it could be better and discuss their individual risk evaluation. Before they start any task, individuals are asked to do their own inspections, walk around, and note any hazards and how those hazards can be mitigated. This information is shared with the supervisor.
The company is going the extra mile in terms of personal protection too. High visibility reflective clothing is now a requirement, and passing beyond industry safety standards employees are now required to wear metatarsal boots. This is being augmented currently by the issuing of metacarpal gloves – between them these two initiatives will go a long way to protecting those vulnerable extremities.
Toes and fingers are the most commonly injured parts of the body. It is important, says Cartwright to address the ‘routine’ hazards as well as the more infrequent but perhaps more serious ones. “We want to eliminate the cuts and bruises while not losing sight of the bigger picture. So we ask employees the question: ‘If you were away from work and heard there had been a fatality at the mine, what would you suspect?’ In other words, what would be the first thing that would come to mind without knowing the facts of the case?” Gut feelings are not always expressed but can provide valuable insight that could save a life, he acknowledges.
The Canadian mines all started out being mined by mining contractors. That made sense for Western, a relatively new company, but Walter Energy’s policy is to bring what is after all its core activity in-house. The last of the Canadian mines to be shifted from contract to company mining was Brule, which has a production capacity of around two million tonnes per annum (tpa). The operation involves two big elements: people and equipment. The mining equipment had to be purchased from the contractor but the personnel could not be transferred so easily.
Most of the management and a large proportion of the supervisory staff left, quite understandably, for reasons connected with continuity of employment and the fact that most of them were not locals, having been flown or driven to the remote site. “In some ways it was a bit like starting up a new operation, particularly from a personnel point of view,” says Dan Cartwright. “We didn’t want anybody to stay who didn’t want to be there. Part of the challenge at Brule is that it is our most remote mine. But it gave us the opportunity to convert to a more local workforce. We still have quite a few drive ins though there are no longer many people who fly in.”
Cost management, productivity and safety ideally go hand in hand. In the current climate, with coal prices well below where they need to be to sustain the higher cost operations, Walter Energy has been stepping up its program of cost reduction. One initiative that has been extended in the last year is its reliability centred maintenance, condition-based program. Reliability-centered maintenance (RCM) and condition-based maintenance practices can extend the duration between routine maintenance, improve unit availability, and eliminate some forced outages, he explains. “We also do sophisticated diagnostics and condition-based monitoring to determine the ‘health’ of key machines and to make sure that we are listening when the machine is telling us work is due.”
As an example, oil changes are no longer just time based. OEMs and agents tend to stay on the safe side when specifying maintenance schedules, but components and fluids can often work far longer before needing to be replaced. Using things like vibration analysis and thermography the condition of the machine can be monitored very closely. The machine rather than just the manual will decide when it needs help!
There was a lot of room for improvement when he took over the job 18 months ago, he admits, but that slack has been taken up. “Our results show in our operations one of the most dramatic cost transitions that I have been associated with in my entire career. We have seen reductions in cost that range between 20 and 50 percent.” But make no mistake, this has been achieved primarily by the application of common sense on the part of the people who actually have to implement it, he insists. “It is our people who make us what we are.”
While emphasising the role of teamwork in safety, productivity, maintenance and lean working, he does not forget those team members who don’t work for Walter. “One of the things we have been doing is to reach out to our partners in the supply and delivery chain to see how we can work together better.” He singles out the Caterpillar dealer Finning, which has been working with Walter to make the RCM work, optimise performance and at the same time preserve its reputation by avoiding equipment failure. “The leadership of Finning in British Columbia has done a really good job in working with and helping us. I believe that our success will be their success in the long run and they recognise that.”
Mines and railroads are sometimes viewed as natural enemies and there’s no doubt a coal mine can be a demanding customer for a railroad. There is tension between the mine’s need to have trains ready to take loads whenever the mine is ready and the rail operator’s need to not have trains waiting. But this can be overcome by better communication and Canadian National Railway (CN) and Walter’s transportation group have done a great job in sharing information. “Both sides are now kept informed so they know our mining plans and we know their plans and commitments too.” He says. “It has turned a good relationship into an exemplary relationship!”
In the end, the steelmakers of Korea and Japan who take most of the BC coking and PCI coal do have other sources to turn to so, the mining companies, the logistics operators and the ports of western Canada need to sell themselves as a united supply chain. The good news is that the railroads and port authorities have been responding to this situation. Westshore, Neptune and Ridley Terminals have recently seen over $1 billion invested in improvements to the efficiency and capacity of their terminals. This includes the addition of more than 20 million tonnes in coal handling capacity. Of all the commodities carried by rail and handled by ports in Canada, coal ranks number one, and an efficient and inter-connected network of rail and port infrastructure is critical to get Canadian coal to market, Dan Cartwright believes.
Written by John O’Hanlon, research by Peter Rowlston