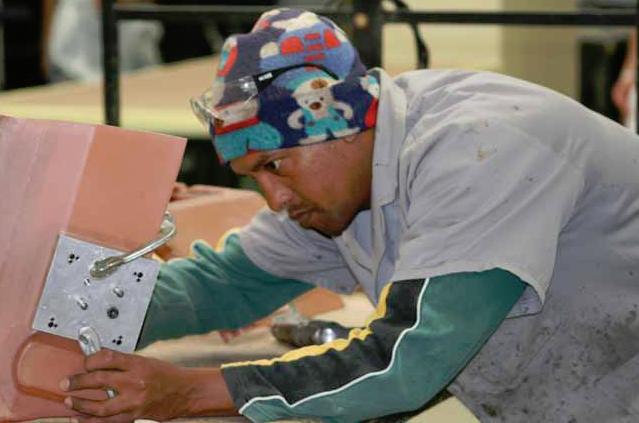
This South African-based specialist in aircraft seating made from composite materials is well-placed to take advantage of the international effort to reduce the weight of airliners.
AAT Composites is a specialist in the manufacture of high-tech, high-specification composite carbon and glass fibre seating components for the airline industry. The company was founded near Cape Town, South Africa, in 1983 as Aerodyne Technology, later becoming Aerodyne Aviation Technology.
Aerodyne established itself as a leader in the design and manufacture of innovative high performance products using advanced composite materials and became well known in the aerospace and sport markets for products ranging from bicycles to primary structures for supersonic aircraft.
Aerodyne was restructured into a group of four companies in the 1990s, with a view to exploring a diversified product and market range. One of these four companies grew into AAT Composites, which now specialises in the design and manufacture of composite parts for aircraft interior structures, mainly seating, although other applications are also being developed.
The company certainly has the right pedigree for seating, with its major shareholder being iconic German seating group Recaro. With customers for advanced aircraft seating rather thin on the ground in South Africa, however, 100 per cent of ATT’s production is exported to Europe and the United States.
The manufacture of sophisticated composite parts can be a laborious process, but one of AAT’s core capabilities is high volume manufacture. The company has a proven moulding capacity in epoxy and phenolic prepreg (pre-impregnated composite fibres) of more than 10,000 items per month.
AAT has extensive experience in the use of prepreg materials, as well as some wet infusion processing. Prepreg processes can be grouped broadly into four categories, autoclave moulding, press-clave moulding, frame moulding and vacuum bag/oven moulding. AAT has four autoclaves in operation, but prefers the press-clave system to meet its high production volume requirements.
Another key attribute is the level of vertical integration which gives AAT control over virtually the whole process from design to final production. The company is involved in the original seat concept, then designs and manufactures its own tooling, before manufacturing the composite parts.
Composite seats have a huge advantage over traditional aluminium seats. Composite materials are much lighter and can be moulded and shaped into configurations that would not be possible with aluminium. Composites save up to 40 per cent mass over traditional aluminium backrests, offer high stiffness and excellent fatigue characteristics, and easy incorporation of video and telephone units.
The material is, however, more expensive to work with and the complex shapes mean that the finishing process is extremely labour intensive, which gives AAT a distinct competitive advantage over European competitors. The company has competitors in China, too, where labour is even cheaper, but AAT outscores them on technology.
The location of a high-tech industry like this in South Africa does present some challenges, however. With very few companies working in the field of composite materials, there is no pool of experienced skilled labour waiting to be recruited, so workers must be trained in-house. AAT has therefore set up its own training academy which takes the workforce through all the practicalities of working with different carbon and glass fibre materials.
A few years ago AAT introduced a lean manufacturing program which has improved shop-floor efficiency and quality. Scrap has been virtually eliminated and customer-related issues have also dropped drastically. Some European customers have made favourable comparisons to the standard of their European suppliers, but the company knows that lean is a process of continuous improvement so there is no let up in its effort.
The training academy has been of great value here, too, providing training in lean manufacturing techniques and world-class manufacturing methodologies. There has been an increased focus on multi-skilling, more time is being dedicated to the improvement process, and there is more freedom to explore new market opportunities.
Composite materials represent a relatively young industry sector, with great long term potential. It’s a vibrant industry, with plenty of ongoing research. Despite the effects of the recession on air travel, there is a huge global effort to reduce carbon emissions in all sectors of the economy. Reducing the weight of items being transported, or the vehicles that transport them is crucial to fuel economy, giving composite materials an ever increasing advantage. With that in mind, AAT is looking at opportunities to produce other components for aircraft interiors from composites and may eventually look further afield than that.
In June 2010, AAT took an expansion opportunity with the acquisition of Advanced Composites Group SA, a South African-based subsidiary of UK-owned Umeco, a composite-materials and supply-chain services company. Also based in Cape Town, ACGSA’s principal business had previously been the supply of tooling suites and composite carbon fibre parts to McLaren Automotive for its high-tech sports cars. That programme has now been completed and ACG decided that the strategic rationale for retaining the business had diminished. With the purchase, AAT acquired full CAD/CAM facilities with a complete five-axis machining capability, supported by state-of-the-art autoclaves and full component trimming and spraying facilities.
AAT has also become involved in what could be the start of something big in the airline industry—seats made from carbon fibre-reinforced plastic (CFRP). The story developed like this: Australian airline Qantas decided to reinvent the cabin interior of its new fleet of Airbus A380 superjumbo passenger jets to improve the customer experience. Renowned industrial designer Marc Newson was enlisted to create a stylish and comfortable interior to include the overall design of the cabin as well as the seating, lighting, lavatories, galleys, furniture and even cutlery and soft furnishings.
Qantas went to Recaro to create a new economy-class seat—streamlined and contemporary but focused on functionality and comfort. Recaro responded with a unique combination: a dramatically thinner profile, innovative comfort features, and a sculpted CFRP seat back with exposed woven carbon fabric to give it a visually stunning aesthetic. The resulting Recaro CL3610 economy seat has been recognized worldwide as an exemplary design, winning the 2009 Australian International Design Award, among others.
AAT comes into the picture with the manufacture of the single CFRP beam that forms the seat’s primary load-carrying structure. Invisible to the passenger, the single-beam design eliminates the traditional rear beam, increasing the leg room between seats but also reducing seat complexity and part count. The beam spans the seat width, providing attachment points for all major seat components and its lightness helps to offset the weight of added comfort features.
Each A380 aircraft has 332 CL3610 seats in economy class and four additional seats for the crew. Qantas is also upgrading its Boeing 747-400 aircraft with new in-flight entertainment and seats, including economy and premium economy seats from Recaro that will feature the same design.
The sky’s the limit. http://www.aatcomposites.com
DOWNLOAD
ATTcomposites_MAR11_emea_BROCH_s.pdf