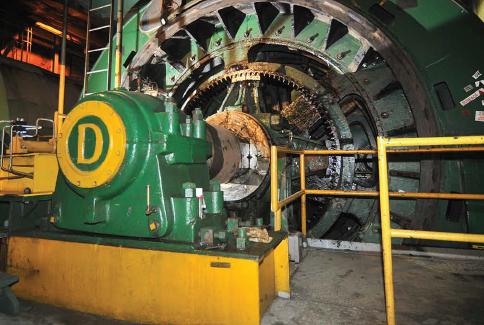
This Canadian engineering company is making its mark in the mining industry with a contribution to energy saving and the environment. Alan Swaby talks to co-CEOs Marc Boudreau and Denis Pitre and to the corporate services/sales & marketing manager Pat Dubreuil.
Aficionados of Doctor Who will be familiar with the Tardis concept – a deceptively small exterior encompassing a surprisingly large interior. In engineering terms, the Canadian company BESTECH is not dissimilar.
Started in 1995 by Marc Boudreau and Denis Pitre, the business initially offered electrical engineering services to the various mining operations found in and around the Sudbury region of Ontario. Since then, though, year-on-year growth in the order of 30 percent per annum has been achieved through the addition of more skills and operating divisions. Now you can find civil, structural and mechanical engineers working alongside their electrical counterparts and providing a full blown engineering and project management package.
With revenue in the $20+ million bracket, the business is small by global standards but in Sudbury it is a senior player, so much so that it is attracting more and more work from Vale Canada, the single biggest mining company in the area. “We are very pleased to have Vale on our client list,” says co-CEO Marc Boudreau, “not least because it is a reliable indicator for other potential customers. We are particularly involved with the Coleman nickel mine, not only providing principal engineering services to Vale for the regeneration of the mine but also working closely with the company’s R&D engineers. This relationship has generated some of the most innovative solutions to engineering problems we have been involved with.”
It’s this development of innovative new ideas that has prepared a platform for BESTECH to spring into a completely different league – and a completely different mix of activities. Over the years, various engineering solutions have been created for specific situations but which have been recognized by the engineering team as having wider applications. All of them share a common theme of monitoring and controlling conditions, using BESTECH’s long standing expertise in the use of programmable logic controllers.
“Electrical engineers not familiar with the rigors of mining life,” says sales & marketing manager Pat Dubreuil, “often completely underestimate just how arduous conditions are below ground and just what control equipment has to face. In order to give our systems the reliability needed, their design – wherever possible – is based on the use of a PLC platform.”
Last year BESTECH reorganized its structure to prepare for the promotion of these new innovative products and services. Dubreuil is charged with the development of this side of the business. “Although, in each case,” he says, “we have a packaged concept that can be offered to customers, there is still a lot of individual engineering that has to go into them. They also take us into an area where we haven’t really been before – in that we manufacture these products in-house, something that has taken considerable capital investment on our part to gear up thoroughly with the technology needed for manufacture.”
The most advanced of these products is a system for adding control into what is often the single largest consumer of energy in mining – ventilation. In development for 10 years, the product is known as NRG1 and the recently released third generation has earned the tag ECO thanks to its energy consumption optimizationcapabilities.
“Hard rock mines in particular,” explains Boudreau, “often spend as much as 60 percent of their energy on running extensive ventilation networks. Without adequate means of control, mines have no option but to run ventilation fans continuously with resulting high levels of waste. They are pushing air around whether or not it is necessary. With NRG1-ECO™ we have shown that annual power consumption can be reduced by 30 to 40 percent compared with a similar sized but uncontrolled system.”
The concept is deceptively simple: conditions in the mine are continuously monitored and the degree of ventilation varied to suit those conditions, allowing ventilation fans to be shut down when not needed rather than being asked to run non stop. However, the exact make up of BESTECH’s controls will vary from mine to mine, depending on the extent of the existing infrastructure and the number of levels that need to be controlled.
If all of this sounds vaguely familiar, it’s true that mines have been attempting to crack this nut for 20 years but until the advent of BESTECH’s solution, there has always been a bit of a “last-mile” shortfall in performance. “One of the special features of NRG1-ECO,” says Pitre, “is our use of open architecture. We use off-the-shelf technology throughout but connect the elements in a way that has not been achieved to date. Furthermore, we can tailor our solution to suit whatever conditions and equipment we find at the mine and can deliver different levels of control.”
Everything that is working in the mine is tagged – equipment and personnel. Then, using a range of proprietary instruments, their location is monitored continuously. As these tagged items move around below ground, ventilation fans in different zones switch on and off to provide ventilation only where it is needed.
Installing NRG1-ECO in a new, greenfield mining development naturally provides the best solution, but the system can be incorporated into existing operations in different ways, depending on what BESTECH’s engineers find. At its most basic level, software can be written around whatever suitable infrastructure exists to make at least some energy savings. Somewhere in the middle, a more elaborate installation based on BESTECH’s ‘black boxes’ will give a new lease of life to old mines by reducing their running costs to a more cost effective level.
The largest installations can cost millions of dollars but in the right hands, they can pay for themselves in about a year. “Under normal circumstances,” says Boudreau, “customers could expect an ROI after three years. But utility companies in North America are doing whatever they can, with government encouragement, to reduce the level of energy consumption. Part of the package we provide is to help customers find the right subsidies and incentives that are on offer which then have a drastic effect on payback time.”
The second product in BESTECH’s line up is also designed to save money but in a somewhat different way. AQM™ (Air Quality Monitoring) is designed to safeguard processing plants which emit contaminants into the atmosphere from crossing the threshold of what is permissible by statuary authority and then being penalized. Those that emit contaminants are obliged by law to monitor the environment and to shut down production should atmospheric conditions threaten to deposit contaminants on residential zones. Systems to do this have existed long before BESTECH introduced AQM, but none of them can match the performance that AQM offers.
“The advantage we have,” explains Dubreuil, “is the ability to collect and make available data in real time with a 99.9 percent accuracy. We have a system installed at the Vale nickel smelter and the plant operators have found it both invaluable and fail proof.”
Every installation will be different, depending on the relationship between the source of contamination, its relationship to residents in the area and the geographical peculiarities of the site. With a good strong flow of wind, contaminants can be dispersed quickly and with very little impact on the surrounding population. However, certain places are more prone to meteorological inversions which bring the smoke plume back down to earth, requiring action on the part of the plant operators.
Predictive models are already used by plants to give an indication of how atmospheric conditions will impact on the plume. AQM provides the supporting evidence of how accurately the model is working.
The Sudbury area network has a ring of 19 monitoring stations that measure emissions such as sulfur dioxide and nitrous oxide. Instead of a PC platform that is susceptible to disruptive power surges, viruses and malware, AQM uses BESTECH’s expertise in PLCs. Plant operators can see in real time how conditions in the atmosphere are shaping up and can adjust the smelter operation accordingly.
“We have decided to market AQM in a different way,” says Dubreuil, “in that we don’t force users into buying an access restricting license. Instead, AQM is web-based and open to as many users as the customer wants. It also means that the authorities can get real time access to the data which makes their supervisory role more effective and timely.”
Another statutory obligation that underground mine owners have is the daily inspection of winding ropes. In order to enable a safer working environment for the miners, BESTECH has brought a technologically advanced solution to the party in the form of RopeInspector™, a remote way of checking the winding rope continuously through the use of cameras and without the need to slow down operations while it’s being done. “With RopeInspector, workers are no longer positioned near moving ropes,” says Boudreau. “Little hands-on work is required with the implementation of RopeInspector, thus eliminating a potential hazardous job. RopeInspector technology also reduces the risk of catastrophic failure. Documentation will be generated, benchmarking conditions, which will enable a supervisor to see the rope deteriorate, hence reducing the risk of danger at the mine site.”
Moreover, daily visual rope inspections with RopeInspector allow mine supervisors to convert inspection time to more productive uses, since the production process is no longer halted to perform the mandated inspections. Production is consequently increased due to the reduction in skip (ore) or hoist (personnel and equipment) down time. “The increase in production opportunities is mouthwatering,” says Dubreuil. “A mine operation’s production value can vary from $1000 to $2000 per minute, so halting production for even 20 to 40 minutes a day can easily amount to lost revenues of $10 million a year. On this basis, RopeInspector pays for itself in just a few weeks.”
Already, this portfolio of products is generating around half of BESTECH’s income and has unlimited potential. For mines and smelting plants in North America, the legal obligations already exist and mines have no option but to comply in one way or another, presenting BESTECH with a steady flow of new business opportunities as new mines are put into production or old ones given a face lift.
The global potential is enormous. With health and safety being a top priority for businesses in the worldwide mining industry, BESTECH products offer effective solutions to address this urgency. “We are offering the global mining industry reliable, high tech and cost effective ways of reducing their operating costs, increasing their productivity and improving overall health and safety,” says Boudreau.
DOWNLOAD
Bestech-NA-Jan12-Bro-s.pdf