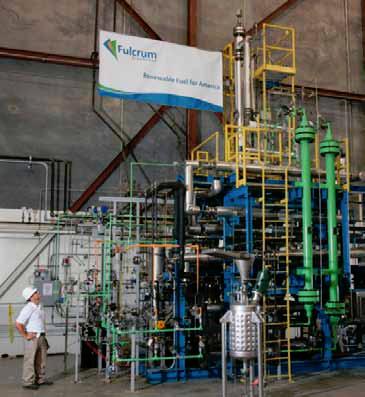
Fulcrum BioEnergy is poised to begin construction on its first facility that will produce ethanol from household waste. Keith Regan learns how this trash-to-energy plant could be the first step toward a network of such facilities capable of producing a billion gallons a year of clean, renewable transportation fuel.
With permits in hand, engineering under way, and equity financing in place, Fulcrum BioEnergy is poised to start construction late in 2010 on what the Pleasanton, California, company sees as the first in a nationwide network of innovative facilities that will transform post-sorted municipal solid waste (MSW)—common household trash—into ethanol, electricity and high-value chemical products.
Sierra BioFuels, as the plant is known, will be located about 20 miles east of Reno, Nevada, and will use a series of technologies and processes that Fulcrum has combined to create what it calls “intelligent biofuel”—ethanol to be used as transportation fuel that reduces dependence on foreign oil and is much cleaner to produce than traditional fuel sources. In addition, the plant will generate electricity to power the facility and high-value chemical products such as propanol, which is used as an industrial solvent and as a chemical intermediate.
“The Sierra BioFuels plant is on track to be one of the first plants of its kind when it enters operations in late 2012,” says Fulcrum vice president Rick Barraza. The plant is the result of work dating back to 2007, when Fulcrum’s parent company, US Renewables Group, formed the firm to make the idea of turning trash into ethanol a reality. “We’ve done a lot of work over the past several years to demonstrate that the technology is clean, reliable and economical—ready for commercial deployment.”
The plant, and others that are likely to follow in coming years, will use innovative processes to make ethanol and other commercially viable end products.
Household trash will be pre-sorted by waste service companies and brought to the plant, where it will be shredded and prepared for conversion through a gasification process that uses extremely high temperatures and high pressure in an oxygen-deprived environment to create a synthesis gas, or syngas, which is made up of hydrogen, carbon monoxide, carbon dioxide and other components. Heat produced during this first stage is used to generate steam used in the plant.
The syngas is then passed through an engineered catalyst that converts it into ethanol, which is then shipped to local markets to be used as transportation fuel.
Barraza notes that Fulcrum has done extensive pre-production work to secure long-term contracts for both the off-take of the finished ethanol as well as agreements with waste service companies to bring enough trash to Fulcrum plants to produce up to 1 billion gallons of ethanol annually. The low cost profile of the process suggests a relatively short-term payback on invested capital. The predictable flow and low cost of the raw material will enable the company to hedge its revenue to further enhance its profitability profile.
“We have a business model that’s very attractive for ourselves and our investors, but it’s also very attractive for the local communities,” Barraza says. Plants are being sited close to existing landfills, which in turn tend to be near large population centers, thus reducing transportation to and from Fulcrum’s plants. “In addition to new green jobs and local renewable fuel production, Fulcrum’s process produces 75 percent less greenhouse gas emissions when compared to traditional gasoline production from oil.”
Leading the team building the Sierra BioFuels plant will be the engineering giant Fluor, which was selected after an extensive review process to become the lead engineering, procurement and construction (EPC) contractor.
Fluor is currently working with Fulcrum’s team on the design of the plant and integration of the various technological components. “We had a lot of interest from firms wanting to be a part of the construction of this project,” Barraza says. “This is something new that has gotten the attention of the industry. Our management team is very excited and believes we have partnered with the right firm that in turn will bring the right people into the fold to help make this project a huge success.”
Fulcrum expects the construction of the Sierra BioFuels plant to create around 550 jobs for the Northern Nevada region, while the operating plant itself will employ between 50 and 60, with extensive automation used within the plant where possible.
The project will be one of the nation’s first large-scale commercial facilities capable of transforming everyday trash into a clean, renewable transportation fuel. Sierra BioFuels will convert approximately 90,000 tons of municipal solid waste—the amount of trash produced by a city with a population of approximately 165,000—into 10.5 million gallons of ethanol and other chemical products annually, meeting the demand for ethanol in the Reno market.
Fulcrum believes the long-term market for ethanol will remain a bullish one, with federal mandates to expand the use of the fuel additive in place. And producing ethanol from trash could become a much more economic and less controversial approach than using corn or even grasses or trees as the feedstock.
Sierra BioFuels should be operating by late 2012, and by then other Fulcrum projects will be moving aggressively through the pipeline as well. “We’ll be producing the ethanol near the population centers where the demand for transportation fuels is the greatest,” Barraza notes. “The more people look at our approach, our technology and our business model, the more we think they’ll become excited about what we’re embarking upon.” www.fulcrum-bioenergy.com