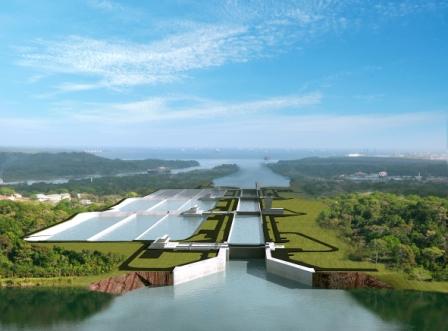
The Panama Canal will celebrate its centenary in 2014. The huge expansion program currently under way should see it through the next 100 years, as Jan Kop and Willmar Muller explain.
The $5.25 billion Panama Canal Expansion Project is Central America’s most visible infrastructure program and the largest project in the canal’s near 100 year history. When it was opened in 1914, it offered a cost saving alternative for shipping to avoid the lengthy route around Cape Horn, and a much safer trip than could be expected through the Strait of Magellan.
In the century since it opened, however, global maritime traffic has multiplied several fold, and the size of vessels has grown well beyond the capacity of the existing canal. It’s a testament to the importance of the Panama Canal to world trade, however, that it has lent its name to the modern definition of ship size—Panamax, and post-Panamax.
The existing sets of locks, which raise ships 88 feet (27 meters) above sea level, define the Panamax standard, which limits the size of container vessels to a maximum of 5,000 TEU (twenty-foot equivalent units). To accommodate the transit of post-Panamax vessels up to 13,000 TEU, and guarantee the future of the Panama Canal as the natural route for international trade, it became clear several years ago that a major expansion program would be required.
The Panama Canal Authority (Autoridad del Canal de Panama - ACP), came into being after the United States finally granted ownership of the canal to Panama on 31 December 1999. In 2006 a national referendum was held in which over 76 percent of the population voted in favor of the expansion of the canal.
The expansion program will almost double the capacity of the canal, and involves several different projects along its 80 kilometer (50 mile) length, including a new Pacific Access Channel to bypass Miraflores Lake, wider channels along its length and deepening of the existing waterway.
The most expensive and prestigious aspect of the project, however, is for the construction of two new sets of post-Panamax locks, one southwest of the existing Miraflores Locks at the southern end of the canal on the Pacific side, and the other to the east of the existing Gatún Locks on the Atlantic side to the north.
Four international consortia were prequalified for the $3.2 billion project and three were involved in the final bidding process. The request for qualifications (RFQ) was issued in August 2007, followed by the request for proposals (RFP) in December. Eighteen months later, the decision was made in July 2009 to award the contract to Grupo Unidos Por el Canal (GUPC).
GUPC is a consortium comprising Sacyr Vallehermoso of Spain, Impregilo of Italy, Belgian dredging specialist and civil contractor Jan De Nul and the Panamanian construction company Grupo Cusa. The ACP announced that GUPC had submitted the "best value" proposal for the new set of locks during a public event held on Wednesday 8 July 2009. This was considered such an important event that it was broadcast live on Panamanian television.
“The ACP had very stringent criteria which included a technical evaluation and a financial evaluation,” said Jan Kop, co-ordination manager for the joint venture and acting project director at the time of the interview. “The technical package was studied first and evaluated; they had a system to award points for various technical subjects, working methods and experience of previous works of comparable scale.” At the 8 July event, the ACP revealed the technical scores and opened the consortia's sealed price proposals. A final weighted score was calculated, constituting 55 percent for the technical proposal and 45 percent for the price submission. “There could have been a possibility that the one with the highest technical score but a lower financial score could have won the contract, but as it happened there was no doubt who was the winner,” said Kop.
GUPC entrusted the conceptual design for the locks project to US-based wet infrastructure specialist MWH Global. “The first part of our contract was to verify that the ACP’s basic conceptual design was viable,” said Willmar Muller, project controls manager for GUPC.
The plan is for two new flights of locks to be built parallel to, and operated in addition to, the original locks, each supported by approach channels. One complication here, however, is the layout of the existing locks on the Pacific side. Currently, ships entering the canal from the Pacific are raised to 18 meters in two stages at the Miraflores Locks, then travel at this level for three miles through Miraflores Lake before being raised an additional 9 meters by the Pedro Miguel Lock.
The new locks have been designed as a single structure, however, which will raise vessels from zero to 27 meters above sea level in three stages at the same location. This means that ships travelling north will emerge from the locks at 27 meters, right next to the lake, which is only 18 meters above sea level. The difference in levels has required the construction of four Borinquen dams—massive, impermeable dykes which have to withstand seismic activity and the potential for grounding of post-Panamax-size ships.
Two dams with a combined length of almost 4 kilometers are needed to form the eastern bank. Two additional dams, with a combined length of about 1.4 km, are necessary along the western bank to keep the canal waters out of the drainage of the Cocoli River.
However carefully designed, with a project of this magnitude the occasional surprise is inevitable. One unexpected challenge in the early stages involved the basalt on the Pacific side which was used in making the aggregate for the concrete. “The basalt behaved a bit differently from how it was envisaged,” said Kop, “which affected our plans and gave us a bit of delay.”
To put this into perspective, it had originally been thought that the basalt for the aggregates, for the Atlantic and for the Pacific sites, would come from the locks’ excavation on the Pacific side, but as the quality was not what was expected, GUPC had to make contingency plans. “We had to open two rock quarries to obtain quality basalt,” explained Kop, “which involved excavating an extra six to eight million cubic meters by drilling and blasting than we originally expected.”
The operations at both ends of the canal have much in common, but there are also significant differences, as we shall see in due course.“Each complex consists of three chambers, so we go from sea level to plus 9 meters in chamber one, plus 18 meters in chamber two and plus 27 meters in chamber three,” said Kop. “That’s the same on both sides. The only additional feature with these locks is that in contrast to the old Panama Canal locks, we are also building water saving basins next to the locks, which allow water to be reused so that waste is reduced by 40 percent.”
Muller added a little more detail. “We have three chambers, lower, middle and upper, and each chamber is 427 meters long and 55 meters wide. The water depth is 18.3 meters.” There is a lot of earth to be moved. An overall 62 million cubic meters, including 8 million of dredging and 13 million of borrow areas are foreseen, plus 26 million of fills and backfills.
“Permanent excavation is about 80 percent complete on the Atlantic side and 70 percent complete on the Pacific side,” said Kop. “To date, we have excavated 16 million cubic meters on the Atlantic side and on the Pacific side we are at roughly 13 million cubic meters.”
The equipment required for this kind of excavation is serious stuff. During the course of the project GUPC has used five Terex & Liebherr 16 cubic meter capacity hydraulic excavators, six Hitachi 7-10m3 hydraulic excavators, and 21 Caterpillar 2-5m3 hydraulic excavators. Thirty Caterpillar and Komatsu 90 ton off-highway trucks have been used, together with another 17 Caterpillar 50-65 ton off-highway trucks, and no less than 54 Caterpillar and Volvo 38 ton articulated trucks.
One of the major differences between the two sides of the project is the nature of the ground. The basalt for the aggregate is found only on the Pacific side, so some of this has to be carried to the Atlantic side for use there. Both projects have secondary crushing plants, but the 3,300 ton/hr primary crushing takes place only on the Pacific side. The basalt is carried six kilometers by trucks to Gatún Lake, from where it is loaded on to 7,500 ton barges for the rest of the journey to the Atlantic project. An added complication is that the Pacific side is located on a fault line, too, so it is subject to earthquake risk.
Another important challenge was that the contract stipulated that the locks would have to be built with concrete that would be durable for 100 years. Achieving the right mix was not straightforward. “We had to do extensive testing to arrive at the desired concrete mixes,” said Kop, “and that cost us some time.”
With most of the excavation work now complete, GUPC is in serious concrete pouring mode. “We are at 23 percent of the 2.2 million cubic meters on the Atlantic side, and 20 percent of the 2.5 million m3 of the Pacific side,” said Kop.
“Our two project teams are carefully watching each other’s performance,” he added. “Last Thursday the Atlantic team achieved 5,000 cubic meters of concrete in one day, which was a record, but it lasted only until the next day as the Pacific project produced 6,000 cubic meters in 24 hours on Friday 29 June. This shows that we are gradually approaching our originally planned average of 85,000 cubic meters per month. Our goal is now to ramp up to 100,000 cubic meters per month on either side.”
If the dimensions involved in this project seem awesome already, perhaps we should look more closely at the electromechanical components—the lock gates themselves. “There are sixteen gates, eight each for the Atlantic and Pacific,” said Muller, “which are being fabricated in Italy by a company called Cimolai.” A series of three locks would normally require only four gates (one at each end and one between each chamber). But this is the Panama Canal, so each gate is doubled, for safety.
“The sixteen main gates represent about 55,000 tons of steel,” added Muller. “They vary in weight from roughly 2,000 to 4,000 tons each. The gates on the Pacific side are heavier as there is more earthquake risk, so those gates had to be designed to withstand earthquakes.”
As well as the main lock gates, there are many smaller gates (valves and bulkheads) which are being built in South Korea by Hyundai. These vary from three to four meters wide by four to six meters in length—and there will be 242 of them altogether. “These will regulate all the water flow from chamber to chamber, between the water saving basins and the chambers and vice versa, and finally to the ocean,” said Kop. “That’s why there are so many of them. These 242 valves and bulkheads represent about 20,000 tons of steel.”
The new lock chambers will feature sliding gates instead of the miter gates which are used by the existing locks.The water saving basins, three per lock chamber, will each be approximately 210 meters wide, 430 meters long and 5.50 meters deep. These gravity-fed basins will allow 60 percent of the water used in each transit to be reused. “The Panama Canal locks are completely operated by gravity,” observed Kop. “There are no pumps to pump water back up.”
The deepening of Gatún Lake, and the raising of its maximum water level, will also provide significant extra water storage capacity. These measures are intended to allow the expanded canal to operate without the construction of new reservoirs.
Engineering and construction have evolved a great deal in a hundred years, so the manpower requirements of the expansion program are not on the same scale as those of the original Panama Canal. “We do not have as many as worked here 100 years ago,” agreed Kop, “but at the moment we have a workforce of some 6,500 Panamanian laborers, complemented by some 1,500 office staff, laboratory staff and so forth. On top of that we have subcontractors with around 2,000 personnel, too.” Skilled labor is a challenge, he admits, as there are several competing infrastructure projects being undertaken in Panama at the moment. The country is fortunate to have an unemployment rate of three to four percent, which in my textbook is pretty close to full employment.
The original completion target for the project was October 2014, to coincide with the centennial celebrations. It now looks like being early 2015 before the works are completed, however, after delays arising from the quality of the basalt, the approval of the concrete mix, and a freak storm in December 2010 which delivered 35 inches of rain in eight days, adversely affecting the excavation process.
The present locks, which will soon be 100 years old, will then be able to give engineers greater access for maintenance, and are projected to continue operating indefinitely. So, the Panama Canal looks forward to its next 100 years.
Written by Martin Ashcroft; research by Dan Finn
DOWNLOAD
GrupUnidos-AM-W4-July12-s_0.pdf