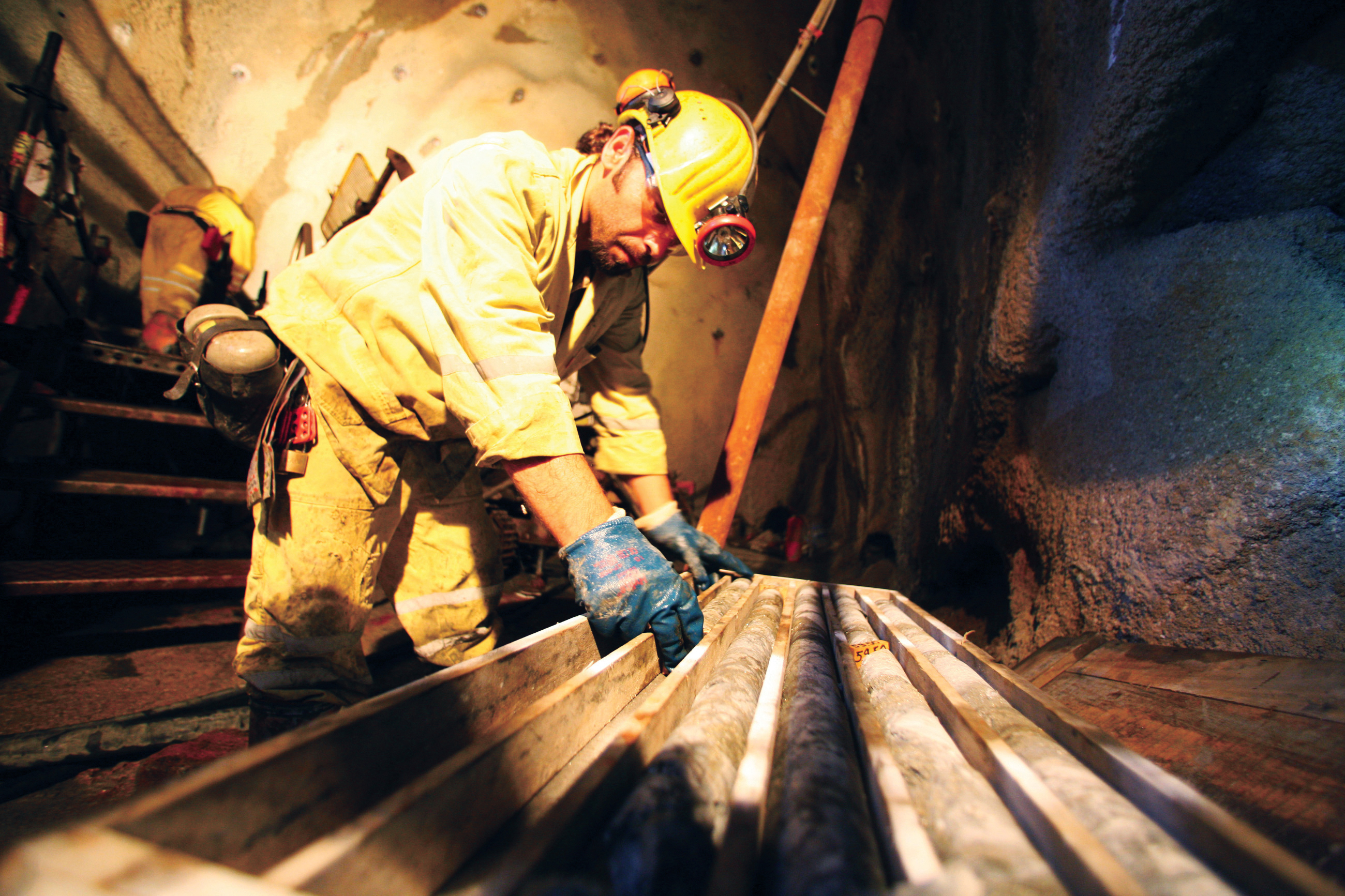
Turkish mine Çayeli Bakir is the only mine in the north-eastern province of Rize. Jane McCallion talks to managing director Iain Anderson about the mine’s recent multi-million dollar capital investment programme and its close relationship with the local community.
Çayeli Bakir is an underground copper and zinc mine located in the north-east of Turkey, close to the Black Sea coast. The facility, a wholly owned subsidiary of Canada’s Inmet Mining, became operational in 1994 and is expected to run until at least 2017.
The mine is located in a unique environment, with the local community living very close to the facility—in fact, almost on the edge of the mine site, says managing director Iain Anderson. While the company is well known in the local area, the mine itself has a fairly small footprint and, says Anderson, most people driving past would not even realise they were close to a working mine.
Çayeli Bakir is a major employer in the area, with 85 per cent of its 490 employees employed from within the province of Rize. However, despite having a ready local workforce, things have not all been plain sailing. “We don’t have a strong mining culture in this area—we’re the only mine in this province,” explains Anderson. “So to support our local community employment support programmes, we’ve obviously had to provide a lot of training for our employees so that we can maintain our standards, particularly on safety and the environment.”
In addition to its undertaking to employ local people, the company’s commitment to the community is evidenced through its active programme to promote local procurement. “We’ve had a number of success stories, such as a local trucking co-operative that hauls our concentrate from the mine site to our port facility in Rize,” says Anderson. “That local co-operative meets our safety requirements and it’s been a real education and learning process for them. They have upgraded their skills and services to provide us with what we need and this has both added value to us as a company and created opportunities for them.”
Çayeli Bakir has approximately 13 major customers located across Europe and in China. “We manufacture and sell two types of ore concentrates: copper concentrate and zinc concentrate,” says Anderson. “We also have an integrated approach to production. Many mines have set up their own mine-to-mill teams; we’re trying to take that one step further with ‘mine-to-mill-to-market’. There are always competing objectives between mine, mill and marketing; so by bringing all of those disciplines together and developing an integrated approach, we’re trying to find that optimum point,” he explains. “And this is one of our continuous improvement strategies.”
Continuous improvement has become something of a watchword at the mine, with a number of programmes implemented to ensure optimum efficiency. “We use a mixture of 5S, lean and six sigma techniques,” reveals Anderson. “We have a number of green belt six sigma project leaders in the company and two black belt six sigma trainers—and this approach has led to a number of improvements across the site. However, we have picked a lot of the low-hanging fruit, so it’s becoming increasingly difficult to identify high value opportunities that deliver a really good return,” he admits. “For that reason, we’ll soon be engaged in a new continuous improvement project, which will be carried out by a consultant. The aim of that project is to identify the value drivers of our business and identify opportunities that might be hidden from us.”
In 2011, the company spent C$15 million on improving efficiencies and conditions underground. The investment was directed into new equipment for production, new equipment for safety and environmental compliance, and new mine management software.
Investment in production has largely been made into sustaining operations. “We’re running an underground mine and conditions there are pretty tough on equipment, so occasionally that equipment needs to be replaced. That means we’re continually upgrading and replacing items such as mobile equipment that we use underground for production purposes,” says Anderson.
One factor that has driven investment in environmental and safety aspects has been the age of the mine. “Çayeli Bakir has been in operation for a number of years and over that time, environmental restrictions on mines have increased,” says Anderson. “So we have acted to bring the mine into compliance with new standards and new best practices and are committed to doing that. Similarly with safety, what was acceptable before is no longer acceptable now.” With safety in mind, the company has invested in a number of new refuge stations in the mine, which are self-contained and designed to support life for approximately 36 hours. Each refuge has its own oxygen supply and has a scrubber system to remove carbon monoxide and carbon dioxide.
The use of PITRAM mine management software, and the implementation of mine control, has also been very important for Çayeli Bakir in terms of improving efficiencies and smoothing the running of operations underground. “Mine control is like air traffic control tower, but in an underground mine,” says Anderson. “In an underground environment, you can’t always see the activity simply because it’s separated by distance. By setting up a mine control room, we’ve given one of our senior supervisors the ability to see the whole mine, to see the big picture, and the ability to co-ordinate our manpower and equipment according to our short-term schedules.
“PITRAM has been the backbone of our mine control philosophy and has led to an improvement in efficiency and allowed us to co-ordinate our resources more effectively,” he continues. “That means that when manpower and equipment arrive at a certain location in the mine, we know that location has been prepared beforehand. Previously, it was being managed by a supervisor in the underground who was trying to juggle the activities in his head—and when you imagine that we’ve got around about 40 people working on any given shift, and about 70 pieces of mobile equipment, it becomes pretty difficult logistically. So certainly, we believe that the implementation of mine control and PITRAM has led to significant and measurable improvement in completion of our activities week-on-week.”
One of the major ongoing challenges facing Çayeli Bakir is the nature of the deposit and the geology of the area. “Çayeli Bakir has been a very successful mine, but it is a challenging mine too,” Anderson comments. “In a number of areas the ground is not very competent and we’ve had to implement a very rigorous ground support regime using rock bolts, cable bolts, mesh and shotcrete to keep areas accessible and protect the safety of people working inside. It has been a major challenge and one that I’m not going to say we’ve overcome—but in the second half of last year we were continually mining in excess of 100,000 tonnes of ore consistently month-on-month, and one of the reasons for that is the ground support regime that we’re using and additional resources that have been allocated. We’ve got on top of a number of areas, but it will still remain challenging for the life of the mine. However, we believe that the techniques we’ve developed here work well and we will continue to refine them.”
While the mine is only projected to continue working until 2017, Anderson is hopeful that further exploration success may mean it can continue for longer. “Mine reserves are essentially defined by whether or not they are economically viable; and that really depends a lot on our cost structure and metal prices. So certainly I think that in that five-year timeframe [until 2017] we have to be realistic; and in the event that we don’t have exploration success or copper prices don’t go through the roof, we will be prepared to address both the environmental and social aspects of closure.”
http://www.cayelibakir.com/en/default.aspDOWNLOAD
InmetMining-EMEA-Mar12-Bro-s.pdf