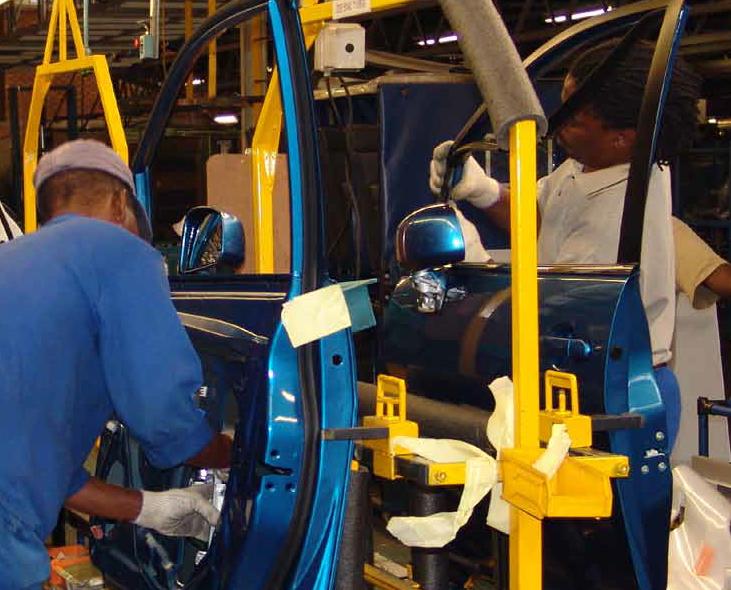
Global automotive manufacturer Nissan is gearing up to double production at its South African plant over the next five years. Managing director Mike Whitfield talks to Gay Sutton about driving up capacity at the plant and localising the supply chain.
Africa is a continent of huge potential. Home to some 13 per cent of the world’s population, it enjoys less than two per cent of the world’s GDP—and those figures highlight two facts: the current simplicity of lifestyle for the majority of the population, and the huge potential for product sales on the continent as that imbalance rights itself.
No one expects the change to be easy or quick, but Africa’s climb to economic parity has already begun and is likely to continue over a long period of time. “While this is not something that will happen in the short term, we believe Africa represents a good opportunity for Nissan, and for anyone, from an investment point of view,” explains Nissan South Africa (NSA) managing director Mike Whitfield.
Global automotive manufacturer Nissan has had a presence in South Africa for over 40 years, and has been manufacturing from the current Rosslyn plant near Pretoria since the site was established in 1963. Today, NSA enjoysnearly a 10 per cent share of the total South African vehicle market, supplying a comprehensive range of passenger cars, light and medium commercial vehicles and recreational and specialised vehicles manufactured in South Africa or imported from sister plants around the world.
The South African operations are managed through two divisions, a commercial division that oversees sales and marketing, and a manufacturing division. Keen to increase its market share in South Africa and across the African continent, the commercial division is working to increase brand awareness and sales through a dynamic programme of new model introductions.
From the manufacturing perspective, the Rosslyn plant is set to play a crucial role in supplying into this expanding market, and Whitfield is driving a programme of improvements that are being rolled out within the plant and out into the supply chain. Over a period of five years, the aim is to increase output from the current level of 50,000 units per year to 100,000.
“Our objective is to maximise available capacity and to prepare the plant for future demand. To do this we have to be very competitive in terms of quality, cost and delivery,” he says. “And we are doing this by rigorous standardisation of all our processes.” This has ranged from the standardisation of shop floor processes, through administrative processes to communications and information flow.
Although improvement at the plant has always been an ongoing process, it was accelerated three years ago in line with the expansion strategy. The improvements are taking place in three key areas. Firstly, the production systems at the plant are being aligned with those in Nissan’s European operations. This is being supported by an aggressive skills training programme; and finally, the entire supply chain is being reengineered and optimised.
“We have put in a completely new production control system that enables the Rosslyn plant to operate on the same principles as those in Europe,” Whitfield says. This has enabled the plant to migrate from the traditional CKD operations, where the plant received complete knock-down kits containing all the parts required for vehicle assembly, to full IPO operations where the plant directly orders the individual parts required for the pre-planned assembly schedule.
As a result, flexibility at the plant has increased considerably. The company is able to control stock levels better and therefore guarantee parts availability. “Our objective now is to continue improving flexibility so that we can react more quickly to market demand,” he continues. “But the degree of flexibility depends on the lead time of the parts, and these can come from any of 12 different countries.”
Improvements in productivity and flexibility are therefore very closely linked with the efficiency of the supply chain, and the company has been making significant changes in this area by optimising the supply chain and introducing just-in-time delivery.
A major element of this change has been to increase the percentage of parts manufactured and sourced locally. “This is an ongoing process, but localisation decisions are being made on an economic basis in terms of total delivery costs to the plant,” Whitfield says. “There are two elements to this: the first is to focus on the cost and quality of the manufactured part, and then the delivery to the plant. Undoubtedly, we will continue to source throughout the world, but our end objective is to ensure we have economic localisation.”
Changes to the automotive manufacturing landscape in South Africa are playing a significant part in promoting localisation. Not only is the government working to establish a strong automotive manufacturing base, but with Ford and BMW also operating in the locality, many global first tier suppliers have established manufacturing plants close by. Meanwhile, NSA has been investing in further manufacturing capabilities. Two-and-a-half years ago, it opened a new injection moulding facility at Rosslyn, and this now makes all the front and rear fenders for models in production.
The company employs more than 2,500 people in South Africa, 1,900 of them in the manufacturing division, and training is therefore an important tool for driving improvement and embedding change. A programme of job-specific training is carried out at Rosslyn on an ongoing basis. Run in conjunction with Nissan Motor Manufacturing (UK), the training is complemented with site visits to the Oppama plant in Japan where staff can experience best practice in action.
At the factory floor level, the company runs an apprenticeship scheme that combines college training with in-house training. “We work closely with colleges to identify potential candidates and enhance their basic skill sets, and then we further those skills with job specific training at the plant.” Then at the management level, a graduate scheme is designed to identify and attract capable new managers for the future. However, with unemployment rife in South Africa there is considerable competition for jobs, and Whitfield sees it as the company’s responsibility to do its part to provide jobs.
“One of the challenges we face in this country is the creation of employment, and we have a part to play in this. But we can only meet the aspirations of the people if we can grow our production base.” There is no doubt that, with the wide ranging improvements across the manufacturing operations and ambitious targets for increased production and sales, Nissan looks set to live up to its social ambitions.