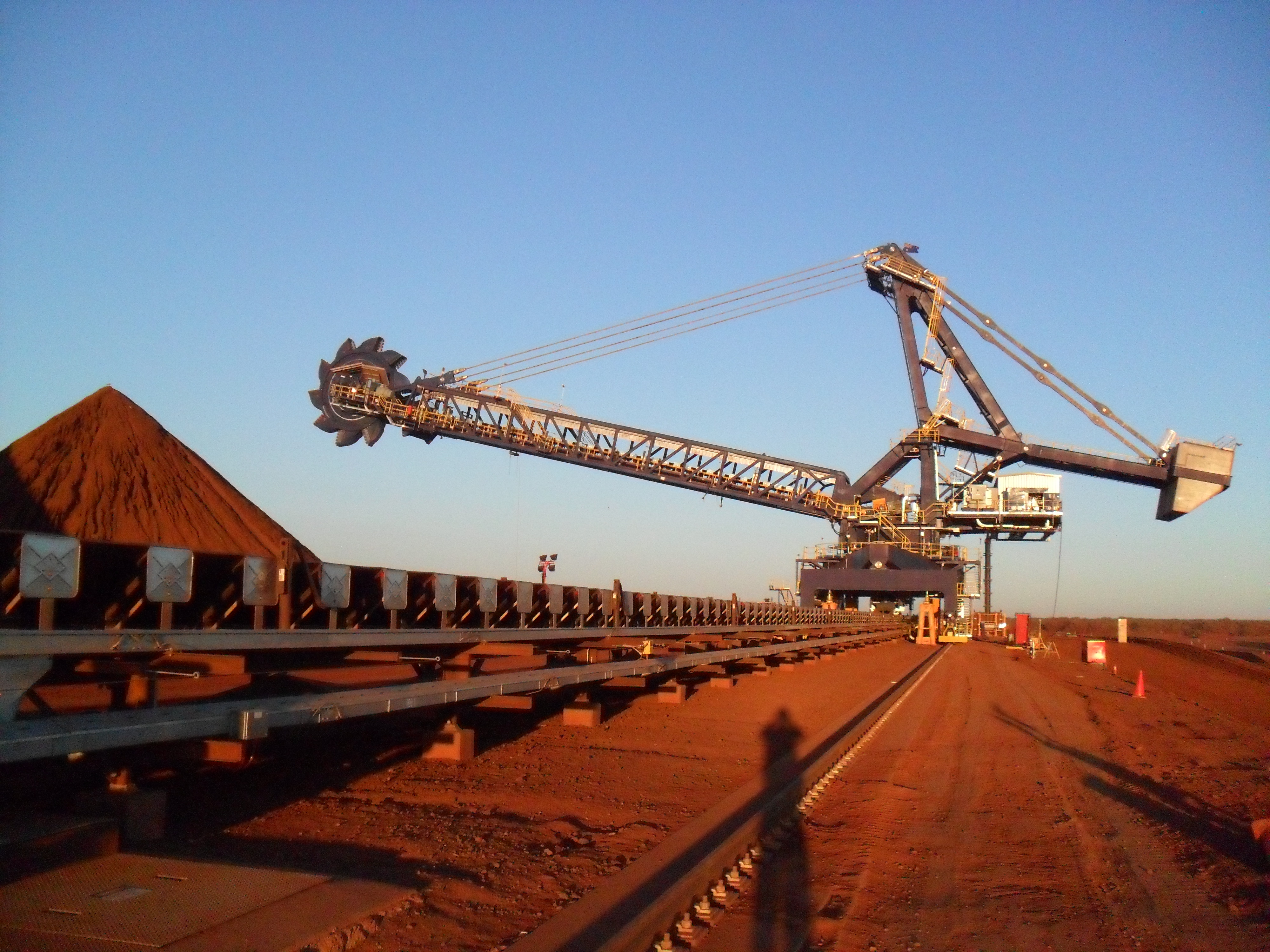
As hardware merchants in the California gold rush discovered, you can make money from mining either by discovering the mother lode or by selling picks and shovels. Jeff Daniel talks to a modern-day version of the hardware merchant.
Any conversation about mining in Australia is bound to involve big numbers—millions of tonnes of ore and coal being dug, transported and crushed, millions of ounces of gold being leached from the rock and billions of dollars invested in new projects. These numbers normally refer to the mining companies themselves but in Australia, there is at least one support company where equally impressive statistics apply.
ThyssenKrupp Materials Handling (TKMH) is a subsidiary of ThyssenKrupp Foerdertechnik of Germany, which in turn is part of the German industrial giant ThyssenKrupp AG, which has an annual turnover in excess of €40 billion and employs an army of 180,000 people worldwide. Its range of offerings covers raw materials such as rolled steel sections, equipment and machinery for the mining industry, processing plants of many different kinds and at the very lightest end of its spectrum, elevators and escalators.
Australia is one of the traditional sales markets for ThyssenKrupp: railway wheels and track systems were supplied there as long ago as 1865. In terms of the global size of the business, the Australian arm is small beer. With a direct workforce of about 150, TKMH generates about €150 million from blue chip clients the likes of BHP Billiton (BHPB) and Fortescue Metal: it is concurrently building stackers, reclaimers and shiploaders for both companies in Port Hedland, in support of their race to increase throughput capacity of the port.
TKMH has also just finished building machines for BHPB’s Yandi mine and Fortescue’s Christmas Creek mine and is presently involved in BHPB’s Jimblebar and Fortescue’s Solomon mine development. These machines are huge, capable of handling up to 15,000 tonnes of ore per hour; and the mines are located deep in the bush, sometimes accessible only via gravel tracks.
The cost of machine erection in those remote places is extremely high. The challenge is to bring the largest possible pre-assembly pieces to site to minimise the actual site work. TKMH has broken new ground here, transporting components of 14 metres in width and 18 metres in height through the bush. The logistics of such a task is very demanding and requires careful planning, even at the initial design stage.
“Another exciting area of development for us,” says managing director Hans Fohlmeister, “is in-pit crushing. With mobile and semi-mobile options available that have capacities as great as 10,000 tonnes per hour, we are able to provide a more cost effective solution for clients who are able to save money on what would otherwise be capitally intensive truck fleets—not forgetting the ongoing maintenance costs. And a significant reduction in carbon emissions is another most welcome side effect.”
Crushing plants and machinery are one of the most fundamental components of any mining operation and few suppliers would be able to match ThyssenKrupp’s range of experience, having supplied this kind of equipment to operations all around the world. Each raw material to be crushed has its own specific features: its size, hardness and abrasiveness, the size of the final product and the expected capacity of the plant all have to be borne in mind in the selection of the most suitable option.
“Over the years,” says Fohlmeister, “ThyssenKrupp engineers have made important contributions to the way mining operations are approached. One of the most significant improvements in open pit mining, for example, was the switch from discontinuous, cost-intensive material transportation by mining trucks to continuous, more economical transportation by belt conveyor systems.”
It was ThyssenKrupp that pioneered mobile crushing plants and now, with several decades of crushing technology under its belt, the company is today one of the most experienced and successful manufacturers of in-pit crushing systems with mobile and semi-mobile crushing plants, mobile transfer conveyors, belt conveyor systems and spreader with tripper cars. The most economic results can be fine-tuned by synchronising the crushing with the mining advance rate and providing a continuous flow of crushed material to the processing plant. Typical ThyssenKrupp installations reach capacities of up to 10,000 tonnes per hour.
The difference between mobile and semi-mobile units is that the first is built ready-mounted on its own travel gear while the latter can still move from one location to the next but as a piggyback load on separate haulage units. Custom designed transport crawlers or common self-propelled modular transporters (SPMT) can be utilised for these tasks.
The choice of which direction to take depends on many different factors but ThyssenKrupp advocates the use of semi-mobile crushing plants when there are long periods between changes of location and especially when working in large and deep open pits and overburden and minerals are being extracted simultaneously from several locations. A semi-mobile plant is equipped with large pontoons which are designed to take up all static and dynamic loads occurring in the structure and which just require the base to allow for certain ground pressures. In most cases, a bed of compacted gravel is all that is required to ensure a suitable foundation.
Today’s mine sites and mining projects demand the fastest possible ramp-up times and optimised equipment installations, and ThyssenKrupp took those challenges into account at the very beginning when designing its latest crushing plant range. It has been its objective to deliver the largest practicable modules to site depending on local requirements and limitations. In some cases, even fully pre-assembled plants weighing nearly 800 tonnes have been shipped to site in one piece.
These design developments bear potential cost savings even if the primary crusher is positioned at a strategic point between open pit and concentrator plant, and thus does not require to be moved to another location during the life of the mine. It has been observed that more and more projects consider the utilisation of a semi-mobile crushing plant as the economically superior option compared to building a conventional fixed concrete structure.
Apart from the size and scale of mining projects in Australia, one other indisputable fact is just how arduous are the conditions. Add the climate to the very nature of the materials being mined and you have some of the toughest conditions that mining equipment has to contend with.
TKMH has two service centres on opposite sides of the country. The main service department is based in the headquarters in Perth, while over on the north-east coast there is a sales office in Brisbane and a service workshop located in Mackay, Queensland.
With support from engineers and designers based in Perth, the service department provides support to customers in all aspects of after sales with a local presence backed by years of experience. Of course, with the vast range of ThyssenKrupp products operating in Australia, it’s not possible to have every spare part sitting on the shelf, waiting to be called upon. The aim then is to provide a totally integrated service between engineering and maintenance and to enable highly trained spare parts technicians, with project management skills, to co-ordinate fabrication projects required as part of the service.
The spare parts department is unique in that it provides a multitude of functions, including manufacturing services. The most effective approach is to have planned maintenance strategies for process plant and equipment when the critical wear components can be changed or serviced with least disruption to production. ThyssenKrupp encourages periodic machine and fixed plant inspections and audit reports for structural, mechanical and controls equipment.
Whether it’s coal, iron ore or gold, mining in Australia is a tough business. You can plan all you want but in the event of an unexpected need, clients have the reassurance that ThyssenKrupp has the means to supply parts in quick time if this is the only way to get production running once again.
DOWNLOAD
Thyssenkrupp-EMEA-Apr12-Bro-s.pdf