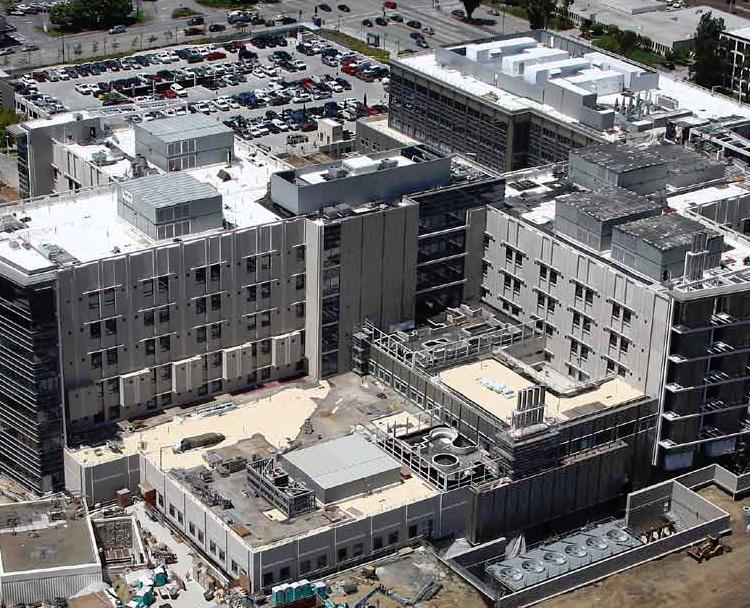
As the Mills-Peninsula Hospital nears completion, executive project manager E.J. Saucier shares with David Hendricks some of the things that went right on the project that might have gone wrong if not for an experienced project team and some creative thinking.
Construction of the new $618 million Mills-Peninsula Medical Center in Burlingame, California, is nearly complete. The 450,000-square-foot hospital, adjacent 185,000-square-foot medical office building and 800-stall four-story parking structure by New York–based general contractor Turner Construction, one of the largest builders of healthcare facilities in the US, have been the result of four years of intensive, often difficult work, involving up to 450 craft tradesmen on site. The base isolation system installed at the foundation of the hospital building should enable the hospital to survive an earthquake up to 8.0 in magnitude and remain operational with minimal or no damage or disruption. It was the first base-isolated hospital in Northern California.
“The biggest challenge with the base isolation,” says E.J. Saucier, executive project manager (based in Oakland), “was the moat, which requires us to have a 30-inch separation from the foundation to the building, and the positioning of exits, sidewalks and stairways in connection to the medical office building was challenging. It has meant about four years of fancy detailing of moat covers and portals, which transport people from the hospital to the office building, as well as weather coverage of seismic joints, all of which we solved with some creative thinking.”
Building hospitals in California, equipping them seismically and so on, is difficult, Saucier points out. “You have to be strong to want to work in this business, and it’s so easy to burn people out, it’s a major concern. In fact, one of the key successes of the project for us was the continuity of staff, working with mostly the same crew and the same managers on and off site. The client was always supportive, and the subcontractors have provided project managers and foremen with the same consistency. That influences the site progress, and it benefits the budget, so in terms of continuity, the overall management was intact. We’re fortunate to be able to retain most of our team right to the finish line.”
Another reason for success is that Turner went with design-assist subcontractors for about 70 percent of the work, and achieving that selection of subs also carried throughout the construction part. The company was instrumental in providing what it called its A-team: experienced, skilled people that worked well together. “Having an A-team is critical,” Saucier says, “because there are so many moving parts in building a hospital, it takes a lot of effort by smart people to put it all together. Every day we run into constraints; it’s the nature of the beast, and the challenge is to be creative and develop work-arounds. Our senior superintendent, Chuck Burda, has been a master in the field for work-arounds. There are many instances of constraints, and if we didn’t have the right attitude and cooperation from others in doing work-arounds to keep the flow going, we’d be stopped in our tracks and frustrated.”
Burda adds, “For example, we had a situation with the generator room, critical to the project. We found that we were stopped because of some sound isolation details that needed redesigning, which prevented us from ordering the final flue section that gated the starting-up of the generator. When we learned that the particulate filter would be delayed two to three weeks, we built a mock-up of the filter, installed that and took our measurements from it so we could then order the flue section and not hold up the job until it was delivered.”
Senior project manager Saptarshi Desai set up a constraint log to identify and catalogue constraints, showing how they were tied to the schedule, and tried to prioritize the information flow. “After identifying the issues,” says Desai, “it was essential to stay in communication with everyone involved. Every week we would meet with the owner, the architect, the subcontractors and Turner staff, and we’d begin by reviewing the most urgent items on the constraint log and arranging them in order of priority, which kept the whole team focused on them in order to maintain the project’s flow.”
On a hospital project the inspection process is extremely critical and timely, in order for work to progress on schedule. This one averaged up to 300 inspections weekly, more than 14,000 in total. Critical inspections are next-day. Freight Train, a construction management software firm in Los Angeles, developed a system to monitor inspections.
Turner used BIM (building information modeling) software to create three-dimensional models of the structures in order to nail down as many coordination issues as possible before going to the job site. “BIM was new to us,” says Saucier, “and to most of the subs, so we all went through a huge learning curve and it paid off—in the accuracy and the productivity of the installation, and it minimized the waste of materials and helped us stay on schedule.” Adds Burda, “One thing that BIM’s 3-D modeling did for us was allow us to increase worker density, by getting a productive workload with a high density of workers. In a normal work environment on a job site like this, there are certain efficiencies in pre-fab and so on, but with BIM, since everything is predetermined and already in place in the model, it takes a lot of the stress out of the field situation when you’re in a hurry. It allows you to increase worker density, which puts more scope into place within a similar time and location.”
Burda further explains, “BIM allocates space and time in sequence. Before we used BIM, we’d start with our biggest components, like ductwork, or the ones with the most difficulty to manage in their space, like gravity drain lines, which must slope at exactly one-quarter inch. You can’t move them up and down like electrical conduit or like pressure water systems. Once those components are in place, everyone else has to cram their work into the remaining space. With BIM, all the coordination of space is done prior to getting to the site, so now you can load the area with workers from the top down, and the work is sequenced, not by degree of difficulty, but by its relationship to the floor. Everything runs smoother and more efficiently.”www.tcco.com