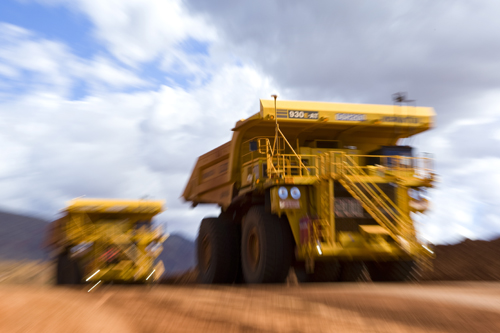
The Pilbara’s red earth, splendid scenery and vast extent combine to create the image of Australia that has caught the imagination of generations. The top-left corner of Western Australia is home to a population that has inhabited it continuously for over 40,000 years; to them it is a very precious landscape. However, today there is another dimension to that value, because the region is rich in the most useful mineral to mankind—iron. Just as the red planet Mars owes its colour to the iron in its crust, so that element reveals itself in the rusty splendour of the Pilbara.
The Anglo-Australian Rio Tinto group leads the world when it comes to the extraction of minerals. Coal, aluminium, copper, diamonds and specialised minerals are all important divisions; however iron ore is in short supply these days and supplying the world’s steelmakers has long been a key activity for the company. It is a staggering fact that roughly 12 per cent of the iron ore consumed today comes from Rio Tinto’s Pilbara mines alone. Though there are other operators in the Pilbara, Rio Tinto’s Pilbara Blend product has a distinct market advantage: by combining the varying output from a number of individual mines, the mills can rely on receiving ore with consistent iron, silica, alumina, phosphorous and moisture content, even at short notice.
And there is no sign of this demand slackening. India and China are both growing at a phenomenal rate and those countries’ consumption of steel for cars, white goods and construction is expected to go on growing, says David Joyce, managing director of Rio Tinto’s Pilbara expansion projects.
To satisfy this demand, China needs reliable supplies at a reasonable cost, and here the comparatively short sea routes to Asia that once made Australia feel vulnerable become an advantage. Already one of the lowest cost producers of ore products, Rio Tinto is embarking upon an ambitious project that will ramp up and streamline production and delivery of the product. Over the next seven years Rio Tinto believes that global iron ore supply additions for China alone will need to find at least 100 million tonnes of additional supply each year, while 500 million tonnes is required to satisfy expected demand growth and 200 million tonnes in lieu of those sources that China would like to replace because of their high cost.
Against these trading fundamentals, expansion in the Pilbara was inevitable. The operations in the region are already extensive, with 14 operating mines, three shipping terminals at the ports of Dampier and Cape Lambert and a 1,500 kilometre rail network. It is a fully integrated system, managed centrally from Rio Tinto’s Operations Centre in Perth. The early prototype of the centre was established in June 2005 as part of Rio Tinto’s Mine of the Future programme, and the fully fledged version now boasts more than 450 staff. “Drawing together the control functions for the mines and the integrated logistics network made it possible for us to produce iron ore at maximum efficiency,” comments Joyce. And that, he adds, was vital to the success of the expansion project.
By 2015 the company expects to have spent more than $A18 billion on expanding the capacity of its Pilbara operations by 50 per cent to 353 million tonnes per annum. As well as mine life extension and expansion of existing mine workings it is driving technology to an extent never before conceived of in the mining industry. Earlier this year, for example, the company committed $A480 million to the introduction of driverless trains—two-and-a-half kilometres long and with a payload of 24,000 tonnes.
The automated trains will be controlled from Perth, as eventually will the fleet of 150 automated trucks being developed in a joint venture with Japan’s Komatsu. It is all about increasing the capacity of the operations to achieve the 353 million tonne target without proportionally increasing headcount. Ten driverless trucks are already working at the Yandicoogina mine in the Pilbara alongside automated rigs that can drill much more precisely than the most skilled human operator, and work faster too because they can return to work soon after blasting, without having to wait for the air to clear. “We have a clear lead on the rest of the world where iron ore mining technology is concerned,” says Joyce.
The object of automation is not just about reducing costs but also about delivering the Mine of the Future, bringing a level of productivity and repeatability that has eluded the mining industry so far, he explains. “The Mine of the Future will demand a new breed of employee: people who can manage highly automated systems and continue to grow those systems. It is about building more efficiently controlled systems that don’t rely quite so much on human elements.”
Rio Tinto’s port facilities are the envy of the other companies working in the Pilbara. Dampier has two ship loading terminals, one at Parker Point and the other at East Intercourse Island, and an associated blending strategy: capacity there has just been increased by a further five million tonnes, at a cost of $A234 million as part of an incremental investment programme to enable the ports and associated infrastructure to handle 353 million tonnes. But the most ambitious port project is to the east at Cape Lambert, where a second 1,400-metre jetty and two-berth wharf is under construction at a cost of more than $A200 million. The new Cape Lambert Port B development includes a tandem car dumper facility, a stockyard including two stackers and two bucket wheel reclaimers, a screenhouse and surge bin facility, a 1.4 kilometre-long access jetty and a double-sided iron ore wharf with two shipping berths and a shiploader. It will be in operation by the end of 2013 and will increase Cape Lambert’s capacity by 53 million tonnes per annum. If and when the second (50 MTPA) expansion is approved, the jetty will be a further 400 metres out to sea and the associated infrastructure will be doubled.
Australia’s national economy grew by 2.5 per cent over 2011, outstripping the Eurozone, and according to the State of the States report, published by the leading Australian stockbroking firm CommSec in January 2012, Western Australia is well ahead of all the other states, largely thanks to its minerals, oil and gas industries. This means there is plenty of work for contractors in the booming Perth region, and securing the best of them for long-term operations in the remote Pilbara has involved some rethinking of the traditional EPCM model, says Joyce. “We have been moving towards framework agreements with our contractors, involving them at an earlier stage to improve planning and integrating them with the entire expansion programme in a way that gives them greater security and the chance to move from project to project.”
As well as reducing cost, the continuity of the framework agreements delivers a safety bonus. And standardisation of design and working methods across multiple mine expansion projects is a further way to cut the overall cost, he adds. “It is a way of putting some formality into our relations with our contractors in Western Australia. We know the construction and contracting market in Perth needs to expand to handle all the work that is being done in Western Australia so these framework agreements are a mechanism to communicate with our contractors and give them confidence to go out and get the people and equipment they need to do this work over the next three or four years.”
This principle benefits local contractors as much as the big construction contractor firms like SKM and John Holland. Since the programme began in 2010 more than a billion dollars’ worth of work has been placed with aboriginal contractors, and Joyce is very proud of that. “We use a variety of models for involving aboriginal companies, of which the most effective has probably been to encourage major contractors to form joint ventures with local contractors.” That way, he says, the local firms can grow and learn by working with their national and multinational peers.
Between 2001 and 2011 Rio Tinto drilled a million metres and doubled its ore reserves in the Pilbara. It plans to drill at an even greater rate over the coming five years, and it will be able to supply its Pilbara Blend customers, at the rate of 353 million tonnes a year, until at least 2045. This is what the Mine of the Future programme is all about: introducing next-generation technologies for mining operations, contributing to better health and safety, production efficiencies and improved energy consumption and environmental benefits.
Written by John O’Hanlon, research by Vince Kielty
DOWNLOAD
RioTinto-APAC.Mining-Mar13-s.pdf