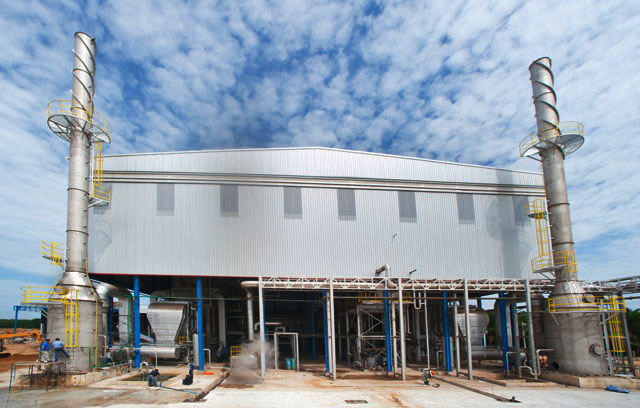
While Macrotek has been marketing pollution control systems to every conceivable industry for more than 80 years – after all it’s hard to name a field of human activity that does not generate emissions – in recent years it has tended to focus on the mining industry. Indeed it has developed a relationship with that industry that could be described as symbiotic. Located in Toronto the company finds itself at the centre of a global technological and financial hub that has made it the city of choice for mining majors and juniors alike. Mining companies like Barrick Gold and Inmet have their headquarters there as do many of the engineering companies like Hatch and Sherritt International that support them.
These are the customers of Macrotek, and the company’s President Peter Ristevski likes it that way – the mining industry is a good fit for Macrotek, sharing his values and the way he likes to do business. “Companies like BHP Billiton, Hatch, Barrick and SNC-Lavalin demand of their partners – and the relationship is one of partnership – to deliver exceptional service, outstanding performance and total reliability. If you can give them that they will stick by you. I have found better levels of loyalty in the mining sector than in any other.”
None of these companies has much use for off the shelf systems. Their projects are highly designed and engineered. “Around 80 percent of the systems we sell are custom designed, firstly to cope with the specific pollutants generated by the application, and also for the customer’s plant. We do not ask the customer to design his plant around our scrubber; we design the scrubber to fit his plant!”
The close liaison between client and niche manufacturer has paid off. When Sherritt brought in Hatch to expand its nickel operations in Cuba the design and delivery of the pollution control systems were given to Macrotek. As a result Macrotek became involved in the much larger Ambatovy joint venture in Madagascar. In that case the lead contractor was Montreal based SNC-Lavalin – Sherritt however specified Macrotek because the requirement was similar. Now SNC is involved in Inmet’s $6 billion Cobre Panama project, just the type of opportunity that will suit Macrotek.
The company aims to grow without incurring unnecessary risk. “Our strategy is to grow organically. We are a private company and definitely don’t want to dilute our interest or, even more importantly, decision making and control.” Macrotek will not seek venture capital or leverage to achieve explosive growth, though that might be an option. It doesn’t need to: growing steadily at a double-digit annual rate it is weathering the recession well with its mining partners.
Having said that, Macrotek is expanding, and as it works increasingly in global markets it is finding efficient ways of dealing with major overseas projects. Increasingly, says Ristevski, it is providing the critical components in which it invests its IP, while doing bulk fabrication on or close to the site. “The Ambatovy units were complex, and high in added value since they had to deal with hydrogen sulphide, but they were small enough to be containerised and shippable in their entirety. But we have done several projects with a boiler company in Thailand, for example, where we just provided critical components, and the fabrication of the stacks and the tanks is done by the customer.” A similar arrangement is being done for an end user in China – critical components and the design of the scrubbers are supplied by Macrotek, while the bulk metalwork will be completed by the US customer’s Chinese partner. “We could not cost effectively ship that heavy stuff to China, but this way we keep control of the confidential components.”
Where large scale contracts are concerned, the market increasingly favours a niche specialist like Macrotek over local and generalist companies that, while they may be competent within their domestic market, struggle to meet ever more demanding regulatory regimes. “Wherever our clients operate they will complete the work to the highest environmental control standards – usually EPA or CEPA for the North American companies and EU standards for the others.”
National emissions legislation varies, but has converged in recent years to the point where there is little to choose between the top-level regimes. The actual standard is specified either by the customer or the funding agency, so World Bank and IMF projects tend to demand EPA while the EU looks to its own set of rules. The effect is to eliminate opportunistic cost cutting by uncertified competitors, he says. “Not many companies can do what we do, or have the capacity to offer the performance guarantees demanded. For example in Ambatovy we had to sign up to performance guarantees backed by a commitment, either a bond or a letter of credit, that stayed with our customer throughout the warranty period.”
But it is not just a mater of doing the job right, important though that is. Macrotek’s R&D is coming up with technologies that can tackle chemical hazards and levels of particulate size that used to defeat all comers. Take the Macrotek Venturi Scrubber, a technology that can remove sub micron dust particles in applications with varying airflows, particularly where abrasive or sticky particulate is being collected. Water is introduced onto an annular disc through a central pipe. The water is sheared into tiny droplets which safely and reliably collect these minute particles.
Macrotek is approaching the demonstration stage with some innovative removal technologies that it will be able to bring to its mining customers, for whom dust is an ever present hazard. But if dust is a nuisance, some of the chemicals the industry works with, particularly arsenic and hydrogen sulphide (H2S), are lethal in small concentrations. “Our aim is to develop technologies that will outperform the most stringent current regulations.”
Hydrogen Sulphide is a highly toxic and inflammable gas. Being heavier than air, it tends to accumulate at the bottom of poorly ventilated spaces. Although very pungent at first, it quickly deadens the sense of smell, so potential victims may be unaware of its presence until it is too late. The lethal concentration for 50 percent of humans is 800ppm for 5 minutes of exposure, and H2S is a by-product in many hydrometallurgical processes. Macrotek has done many systems for some of the major multi-national mining giants all over the world and has developed a unique two-stage process that has been successfully applied to several of these systems. Macrotek’s packed bed scrubbers are a highly efficient way to absorb gases using a high efficiency mist eliminator, and the company is working on advanced systems that will target H2S and arsenic in particular. “Conventional hydrogen sulphide removal technology comes at very high operating cost. The reagents are expensive, they are not regenerative and the disposal of the by-product is expensive,” explains Peter Ristevski. “We shall soon be demonstrating a new regenerative type of metal catalytic reagent that could reduce operating costs by 50 percent.” The technology is expected to be released in 2014, and will represent a huge opportunity for the company, he says.
With no slowdown in the mining sector in sight, Ristevski is optimistic about the future of Macrotek. It will thrive as long as it continues to produce customised solutions for its worldwide clients, optimising energy efficiency, exceeding regulatory requirements, and delivering results unique to each environmental need – and these are standards it will never compromise.
Written by John O’Hanlon, research by Robert Hodgeson