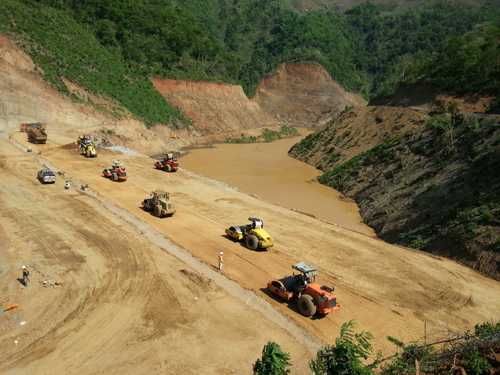
Analysts talk of Vietnam becoming the fastest growing Asian economy, reaching a ten percent growth rate within the next twelve years with one of the main drivers being its natural resources. The country has significant known deposits of many bulk and niche minerals, including bauxite, rare earths, tungsten, titanium, phosphate, coal and iron ore but with the exception of its coal most current mining operations are on a small scale. There is a huge opportunity there for large-scale development, since the mining industry currently contributes only two percent of Vietnam’s GDP, if oil, gas and coal are excluded.
Nevertheless, with China on its northern border Vietnam has to be in the best place to supply the mineral needs of its powerful neighbour. For these reasons there was bound to be a lot of interest in the country’s first nickel mine. Asian Mineral Resources (AMR) listed on the Toronto Stock Exchange’s Venture Exchange in 2004, focusing all its efforts on developing the massive sulphide nickel resource located on what is now identified as the Ban Phuc Project Area located160 km west of Hanoi in Son La Province, in north-western Vietnam.
There’s no need to dwell on the period from October 2008, when metal prices fell and work was suspended until market conditions improved in 2012 and the project could be restarted. Since the end of last year all systems have been go, aiming for first production in June 2013. “We are flat out finalising construction of the process plant and the infrastructure to support that,” says AMR’s CEO Simon Booth, who has moved to Hanoi to oversee progress of the company’s 90 percent owned subsidiary Ban Phuc Nickel Mines (BPNM). “Our activities are very much focused on getting the plant operational, and restarting the underground operations next month, leading to the opening of the processing plant at the end of June,” he says.
The mine represents nothing less than the start of a new industry, and while there is a limited amount of expertise in the country, the Vietnamese are hungry for additional skills. “The mining industry is not a well developed industry here,” he explains, “but that said every mine presents its own challenges of drawing on the national expertise and talent and developing that. We are bringing in a number of trainers from overseas to train up the local workforce, though the general level of education here is high, and there's a strong will to acquire new skills.” If specialised mining is something of a new area, a strong engineering base exists in the country. It is just a question of taking those skills and moulding them to what is required on a mine site, he says.
Currently the progress of the mine sounds frenetic. As the finishing touches are made to the process plant, the infrastructure to support it – the power connection to the national grid for example – is being installed and tested. The tailings storage facility is being prepared, and at the same time preparations are going ahead for the recommencement of underground operations in May, so that there will be some ore ready for processing when the mill opens at the end of June. Once built the ore processing plant is expected to process 1,000 tonnes of run-of-mine ore per day to improve its nickel concentration from 2.2 percent to 9.5 percent. The process plant consists of a crusher, ball mill, classifiers, flotation cells, thickeners and filter press.
Before the mine was put into maintenance mode nearly a kilometre of underground development and shafts had already been prepared, Booth points out, so this is not like starting a mine from scratch. “We have already intersected the ore body on two different levels, so much of the hard part is already done.” Concentrate from the mill will be packed in two tonne bags for ease of handling and transportation, but also to reduce dust. Then it will be taken by truck from the mine site to the port of Haiphong and sold to the international market through a Hong Kong based commodities trading group.
In the immediate vicinity of the mine the majority of the people available are either unskilled or semi skilled. For technicians it is usually necessary to spread the net wider, throughout Son La Province or beyond. If they can’t be found in Vietnam, then they are brought in from abroad. There’s a core of people who were working with AMR back in 2008, and who are very keen to get back into the saddle. For the rest, an intense training programme started at the end of 2012. “They are doing very well under our expat training team, which includes one trainer that we recruited from a mine in Laos. It has been very much easier for him to understand the culture here and the key tasks that are needed to build a successful training programme.”
The programme uses recognised training modules that have been translated into Vietnamese. They are learning to operate some very sophisticated machinery controlled by PLC (programmable logic controller) systems accessed by HMI (human-machine interface) with output that is largely numerical and graphic so language is less important than the ability to read figures. Having been involved pre-2008, another contractor Aurecon is returning to provide electrical, and control and instrumentation design as well as engineering, procurement and construction management (EPCM) services for the process plant, slurry line to the tailings dam, and potentially the underground mine.
At the time of writing there are around 250 people working on the site, but once the mine is in full production numbers will rise to around 400, perhaps 10 percent expatriate. The actual mining operation will be carried out by a specialist contractor from Australia. Mancala was appointed in December 2012 under a three-year contract to supply the underground mine with development and pre-production personnel, mine equipment and management services to develop and mine some 350,000 tonnes of ore annually. The company is bringing in its own expert trainers, however it aims to have a largely Vietnamese workforce within six months. “The best thing in underground mining,” says Booth, “is to keep it simple. This is an operation that will be raising standards in safety, health, environmental performance and in the way it looks after its community and it will be a proud place.”
Though the resource as defined at present will support commercial mining for around six years with more than 200,000 tonnes of nickel and copper concentrate, its extent could be considerably greater – with a consequently longer mine life. “It has very good exploration potential, and geologically this is a very attractive area for new nickel resources to be located,” says Simon Booth. “We will recommence drilling after we commission the process plant, and I can see AMR operating in Vietnam for a great deal longer than just six years.”
Written by John O’Hanlon, research by Richard Halfhide