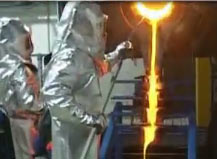
Lapland might be more commonly associated with Santa Claus than mining for gold, but this is where one of the largest gold deposits in northern Europe is to be found. Known reserves at the Kittilä Mine already contain more than four million ounces and there is a strong probability that much more will yet be found in a series of deposits running along a 25 kilometre trend. The mine is located approximately 900 kilometres north of Helsinki and 150 kilometres north of the Arctic Circle. Its first gold was poured as recently as January 2009 and commercial production began four months later. Three thousand tonnes of rock a day must be crushed and processed to extract a yield which is currently in the region of 150,000 ounces of gold a year. Kittilä is the furthest north of all the mines in the Agnico-Eagle portfolio and is worked as an open pit mine at present. However, the mine’s general manager Carol Plummer is quick to dispel images of empty frozen tundra. “In fact, the temperature here is much more moderate than that found in northern Canada. The Gulf Stream from the Norwegian coastline has a moderating effect, so even though we are well within the Arctic Circle, there are trees and shrubs which you might not expect to find,” she says.
Battling with the cold is much less of a challenge than finding the skilled people needed to operate the mine. “Finland has a strong mining history, but has had fewer operational mines in recent years, so there is a lack of experienced engineers. We are heavily involved in a whole range of training initiatives and we are very supportive of the University of Helsinki, which is doing an 18 month conversion course to give engineers from other disciplines the skills necessary to adapt to mining,” she explains. Language is another major challenge for this English speaking manager, particularly in a highly technical environment where health and safety must always be a priority.
“The site has two full-time translators and a multilingual management team. It is critical that we understand each other—the terminology we use is not something that can be looked up on Google. Just sending out an email can be a challenge because our use of language has to be precise and fully understood by everyone,” she comments. As well as the site’s excellent safety record, Plummer is also proud that the mine is working to exceed government environmental guidelines in the management of the waste rock it produces. “We have a very competent environmental team in place and aim to have as little impact as possible.” Open pit mining is well established; and Plummer expects to see production start on underground reserves Later this year. “We are currently undertaking a feasibility study and so far the results are encouraging. Geologically, there is still a lot of open territory and we keep increasing our estimates of the reserves.” At present there are more than 200 contractors on site, most of whom are attached to one of the 11 diamond drills that literally spearhead the exploration.
A further 300 people are directly employed by Agnico-Eagle. Extracting gold might not be about medieval alchemy, but it is still a complex and demanding process, particularly in this instance, where geology dictates that the rock does not easily give up its prize.
“Each tonne of rock yields on average 4.8 grams of gold,” she states, before going on to explain the series of processes needed to extract the precious metal. “First, we must move the rock to the processing plant where it is broken down in the crusher to pieces less than six inches in diameter. Then it is ground into a powder. We rely on a standard flotation separation method, whereby we add a chemical that causes the gold bearing particles to be attracted to air. Air is then bubbled through so the gold bearing ore floats to the top of the tank whilst the waste material sinks to the bottom.” Unlike the company’s other mines, there is refractory rock at Kittilä, which means that the gold cannot be simply dissolved in leaching tanks. “It must first be subject to high temperatures and high pressure in order to break down the sulfide minerals and release the gold and then it can be treated with the normal extraction method,” explains Plummer. “We end up with a high grade sludge which is then melted in a furnace before being poured as gold bricks. However, to give near total purity, it must then be refined even further—but that is not something we do on site. ” Plummer points out that one of the advantages of being part of a larger group is the sharing of best practices, both from a technical perspective and from the point of view of developing human resources. “For example, our supervision formula was pioneered in Quebec and is used by the Agnico-Eagle mines there. As a group, we have developed a very specific way in which we want our managers to supervise and communicate. A standard approach and a common communication tool ensures that engineering or maintenance personnel are immediately informed of anything unusual or out of the ordinary. It is important for productivity, but above all for safety that all our supervisors work to the same high standards. There are very clear guidelines in place regarding what should be verified and checked in each operation with specific check lists for each task that must be undertaken.” Looking to the future, Plummer points out that the mine is in its infancy and has enormous untapped potential. “Already we have 26 million tonnes of probable mineral reserves identified and we know that there is much more yet to be identified. This is what all our exploration efforts are geared to finding out. We don’t yet know what the limit is—only that it is still a long way off,” she concludes.
– Editorial research by Daniel Finn