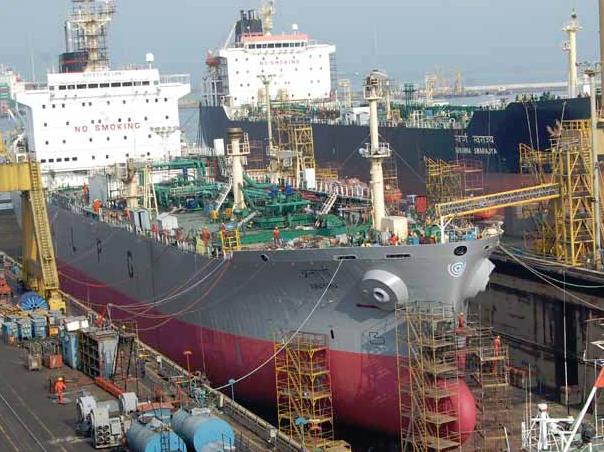
The Port of Colombo in Sri Lanka is a stone’s throw from the main east-west shipping route between Australia, the Far East, Europe and the Gulf oilfields—perfectly placed to catch the passing trade.
Sri Lanka has fantastic advantages of geography. It commands the west and east coasts of its teeming neighbour India: sea traffic round the Indian subcontinent has to skirt its southern tip, as does the long haul bulk cargo, tanker and container traffic that plies between east and west. That gives Colombo, Sri Lanka’s commercial capital, a strategic advantage that can’t be taken away; but in recent years there has been a falling away in demand for the facilities at the port, and in particular Colombo Dockyard, despite its considerable expertise and excellent facilities.
It’s no secret that until recently Sri Lanka had been racked by internal strife for nearly 30 years. The conflict made shipowners wary of entering service arrangements with the dockyard as insurance premiums were raised, says Mangala P B Yapa, CEO and managing director of Colombo Dockyard. That conflict was comprehensively resolved a couple of years ago, and the way finally laid open for Colombo to take its rightful place in the maritime service industry. “Sri Lanka is now one of the freest and least troublesome areas in the world to carry out ship repairs,” he claims.
The Colombo Dockyard Company is 35 years old, which means that it has operated for most of its life under war conditions—but it has still managed to grow consistently through that time, says Yapa. “That proves the operational efficiency, good management and competence of all the people involved. If they are given the opportunity to perform in a free environment following the war you can just imagine what we can achieve!” The fact that a controlling share in the business belongs to Onomichi Dockyard Company of Japan is another help, he adds. “We have a people-oriented environment, and operate Japanese principles like kaizen. But we are not trying to recreate what Japan has done so much as to learn from them and work out what we can do in Sri Lanka with similar thinking.”
Colombo Dockyard employs 1,300 people, supplementing them with contracted labour as needed. Of these, 500 have been trained in shipbuilding at Onomichi—shipbuilding is an important activity at the dock, though until 2005 it built only for the local market. “In 2005 we decided to take advantage of the boom in shipbuilding and go out to external markets. Now we have the capacity to build vessels of 100 metres and more in length. We can deliver four vessels a year and we are working to increase that to six.”
In October 2010 the dockyard delivered the second of two passenger/freight vessels for the Indian government. And last year it also started work on the first of two 68 metre anchor handling tug supply vessels for Samoa. Highly technical and specialised ships like these are increasingly required in support of oilfield operations, and they can now be ordered with confidence and at a very competitive price compared with dockyards in other parts of the world, he says. “We have built nearly 10 vessels since we started in 2005, including two passenger vessels, four anchor handling tug cum supply vessels, two multipurpose supply vessels and two ROV platform support vessels.”
The dockyard is also to deliver two high powered anchor handling tug cum supply vessels with 150T bollard pull capacity to Singapore owners, while three more improved versions of ROV/platform support vessels with oil recovery facilities—an improved version of the ‘R’ class that the dockyard has already built and delivered—are being constructed.
Colombo has four dry docks ranging from 107 to 263 metres in length; however, much of the traffic to Colombo these days is made up of container ships. These ships normally dry dock at their destination ports either in Europe or the Far East, says Yapa. “Colombo is not a terminal port, so they put in here either laden or half full. But we recently launched our Afloat Repair unit to provide all the engine room, electrical and electronic, piping and deck work—anything at all for which you don’t need a dry dock.”
These container vessels call at Colombo every two weeks or so, he continues. “We can have components waiting and install them at the next visit. We can even put repair personnel on board so the repairs can be carried out while the vessel is on the way to its next port of call. The advantage is that we have a duty free facility so all these things happen without attracting any custom duty, and that includes spare parts. An owner who has a fleet of container vessels plying to Colombo can keep his spare parts stored at Colombo Dockyard without paying any custom duty.”
The dockyard is in partnership with OEM service providers: for example, Wärtsilä has its own service company in Colombo which is mainly catering for the power generation sector. Caterpillar has its own service agency, as do MAN B&W, ABB, Cummins, Hydrex and Yanmar. For example, if a ship’s Wärtsilä turbocharger requires balancing the dockyard will remove it from the ship, send it to the Wärtsilä factory where it will be tuned and balanced then re-install it. “The Wärtsilä guy will come and commission it, and the ship can depart with minimum delay.”
No longer a risky place to carry out such repairs, Colombo is now seen as a better bet than rival yards in the Middle East, which following the unrest of recent months might now be perceived as being less stable than Sri Lanka—or indeed Singapore, which is becoming very expensive and is having skills problems. Most of the work done in the Singapore yards is carried out by contract labour, often underpaid in defiance of Singapore’s strict labour regulations. Quality has been seen to suffer as a result, he says.
Circumstances have come together to provide a real opportunity for Colombo, Yapa concludes. “Being a developing economy means our labour and management costs will be lower than either Europe or the Far East. We have competent, directly employed people who can go on board and do the job but it is not just a question of manpower. We have a sophisticated IT system; our dockyard systems are ISO certified so we can offer a fully integrated stock management system so the owners will see how their stock is moving; and we can come to long term service agreements so there is no need for a superintendent on location constantly negotiating each job.”
The odyssey of excellence continues... www.cdl.lk