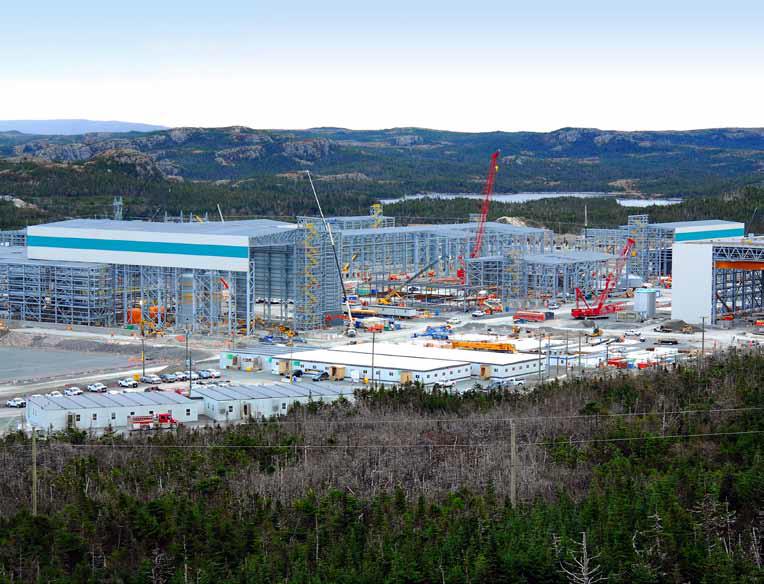
Exploiting Canada’s mineral riches is encouraging new technologies to be put to the test, as Alan Swaby learns from general manager Long Habour Operations Don Stevens, Long Harbour Processing Plant construction project director Rinaldo Stefan, and corporate affairs manager Bob Carter.
There are two things an ambitious engineer wants to see on his CV: big projects and ground breaking technology. For those lucky enough to be working for Vale on the Long Harbour project in Newfoundland, they will have both.
Formed in 1942 as a publicly listed but government-owned engineering concern, Vale has played a major part in Brazil’s development, primarily – but not exclusively – through iron ore mining.
At the time of privatization in 1997, Vale had a limited global presence. Its 11,000 strong workforce was confined to operations in Brazil and the United States, along with a handful of offices in the Far East and London. Now, however, it’s the world’s second largest mining company after BHP Billiton. There isn’t a corner of the globe where minerals are to be found that doesn’t feature Vale, and the workforce has grown over ten times to 120,000 in over 30 different countries.
Vale’s interests have diversified and today it holds the distinction of being the second largest nickel producer anywhere; a situation that came about largely through the acquisition of one of Canada’s largest mining companies, Inco, in 2006. Canada is particularly rich in nickel. Around 30 percent of the world’s needs are met by Sudbury, Ontario, where nickel has been mined for over 100 years. One theory is that the nickel in the ground rose to the surface following a meteorite impact in the area, early in the earth’s geological history.
Compared with the millions of tons of iron ore that are extracted annually, the production of nickel is on a much more modest scale. Vale, for example, accounts for about 250,000 tons, destined for the metallurgical sector where its properties of resistance to corrosion and ductility are used in the formulation of stainless steel and other alloys.
Whether brought to surface by meteorites or not, nickel occurs most often in combination with sulfur and iron. There are several ways of extracting the nickel depending on the exact composition of the mineral bearing rock but until recently, they all involved smelting and used considerable amounts of energy to reach sufficiently high temperatures to release the nickel.
Vale’s most recent nickel venture is located at Voisey’s Bay in the Canadian province of Newfoundland and Labrador. Voisey’s Bay is on the north coast of Labrador and 1,200km away from the provincial capital of St John’s on the island of Newfoundland.
“Nickel was found there in 1993,” explains corporate affairs manager Bob Carter, “and it is viewed as one of the most important nickel-copper-cobalt discoveries of recent times. It has been estimated that there may be as much as 60 million tons of resource contained in near surface and underground deposits. We currently have a mining plan based on the near surface reserves which has a working life of 15 years.”
The mine processes up to 6,800 tons of ore a day from which it produces nickel and copper concentrates. The copper concentrate is sold into the market and the nickel concentrate is shipped to Vale’s operations in Sudbury, Ontario and Thompson, Manitoba for further processing. Vale ships the nickel concentrate on a purpose built Arctic-class bulk carrier especially strengthened to break through the sea ice that builds up in the waters around Voisey’s Bay.
An integral part of Vale’s agreement with the Government of Newfoundland and Labrador requires that processing be done within the province. The question then, is what form of processing?
The answer is to be found at Long Harbour, 100km overland from St John’s, on the Avalon Peninsula. “Vale’s R&D engineers had been looking for a more efficient processing technique for nickel since the late 1990s,” says Don Stevens, general manager of the Long Harbour project. “They decided to take a fresh look at hydrometallurgy – a well-established process that uses water based chemicals to extract metals from minerals. It’s a technique that has been used for 50 years but has never been applied to sulfide bearing rocks.”
Rather than look for something entirely different, the approach was to use proven hydrometallurgical methods but link them up in a novel way. As well as requiring less energy input, hydromet has a major environmental advantage over smelting since most of the waste products from the process are not produced as air emissions, but rather as solids, which can easily be contained.
In conventional pyro-metallurgical smelting, sulfides are burnt off, creating SO2 gas, which is released as air emissions. With hydromet, there are no air emissions. The sulfides are transformed into elemental sulfur, which together with iron oxide form solid tailings. The tailings will also contain gypsum and unleached rock minerals and they are eventually neutralized to form a stable residue.
After several years of lab work, the R&D team put the concept forward together with estimates for a mini-pilot plant in Ontario that would take the bench research to a 1:10,000 scale. The next step was to build a demonstration plant at Argentia (close to Long Harbour) using actual Voisey’s Bay concentrate, to allow for fine-tuning and optimization of the process. Construction of the 1:100 demonstration plant began in 2004 and the plant ran until 2008.
By then, the $200 million R&D program had been deemed a success and approval was given to build the Long Harbour installation. This time, though, the price tag would be US$3.6 billion and require a 700 strong army of engineers just to complete the design details.
“Under the terms of our arrangement with the provincial government,” says Rinaldo Stefan, project director for the construction of Long Harbour, “we are obliged to have a processing plant in operation by 2013 and we are on track to meet that deadline. There are just loose ends to be tied up with the engineering and most of the civil work is complete which means construction is about 50 percent complete.”
The entire site comprises two distinct parts: the port facilities where nickel concentrate from Voisey’s Bay will be received and 3km inland, the processing plant itself which has a footprint of 1km x 750m. “At the height of construction,” says Stefan, “we have a workforce of 3,500 working on the site or preparing material at other locations. Fortunately, as many of our people are coming from or staying in St. John’s – about a 1 to 1½ hour commute – the site itself ‘only’ has to accommodate 1,000 of them.”
As Newfoundland is an island on the edge of the Atlantic and at the mouth of the Gulf of St Lawrence, everything for the project has to get there by sea. Modules measuring as much as 30m x 20m and weighing up to 350 tons are being pre-assembled at offsite module fabrication yards and shipped to Long Harbour by sea. It’s a pretty aggressive schedule that the logistics teams have set. In April, for example, 12 module deliveries are expected but schedules can easily be disrupted by unpredictable weather like gale force winds that can blow for up to a week.
Although the site seems large, it will in fact be completely filled by 16 different buildings and miles of connecting piping, so there is precious little spare space available there for storing material. Fortunately, within a short distance there is a former naval base which is being used as a transshipment and storage center.
“Although the individual processing steps used in the technology are proven,” says Stevens, “the flowsheet on the whole is novel, very complex and involves around 5,000 key components. Therefore, the planning and logistics and the systems employed to control the flow of information and materials have to be faultless. Just as critical is the selection and relationship we have with contractors.”
However grand this project is, it’s not the only one being undertaken in Canada where the mining and oil and gas industries are working flat out opening new developments. So demand is running ahead of supply in every conceivable way. “There is such a lot of work out there,” says Stefan, “that contractors are being picky about what they bid for. Rather than breaking the work down into small sections, we are having to bundle large blocks together to grab the attention of contractors.”
Nor is it easy to find suitably qualified tradesmen or engineers on the doorstep. Newfoundland has at best a population of 500,000 and the province has been without a mega project for some years. Consequently, the skills base has shrunk through retirement and migration. At the same time, Vale is having to compete with many other mega construction projects in less inhospitable parts of Canada (and the world for that matter) for what talent remains.
Nevertheless, as long ago as 2002 Vale identified a group of key R&D individuals to stay with the project from start to finish. They were involved with the process design, helped run the mini-pilot plant and demonstration plant and later were embedded in the engineering team. As such, all the R&D knowledge has been incorporated into the nuts and bolts design and will continue to stay with the project well into the production proper.
Construction is due to finish in mid-2013 and commissioning will begin towards the end of the year. By summer 2013, the plant is expected to be ramping up but it will be some time before it functions at its optimal level. “Scale up is always a risky process,” says Stevens. “Going from research stage to a functioning plant – however small – is a big step. The challenges of building and operating a 1/100th scale demonstration plant were great. Now we are doing it again, this time a gigantic step into new territory.”
DOWNLOAD
Vale.LongH-AM-May12-Bro-s_0.pdf