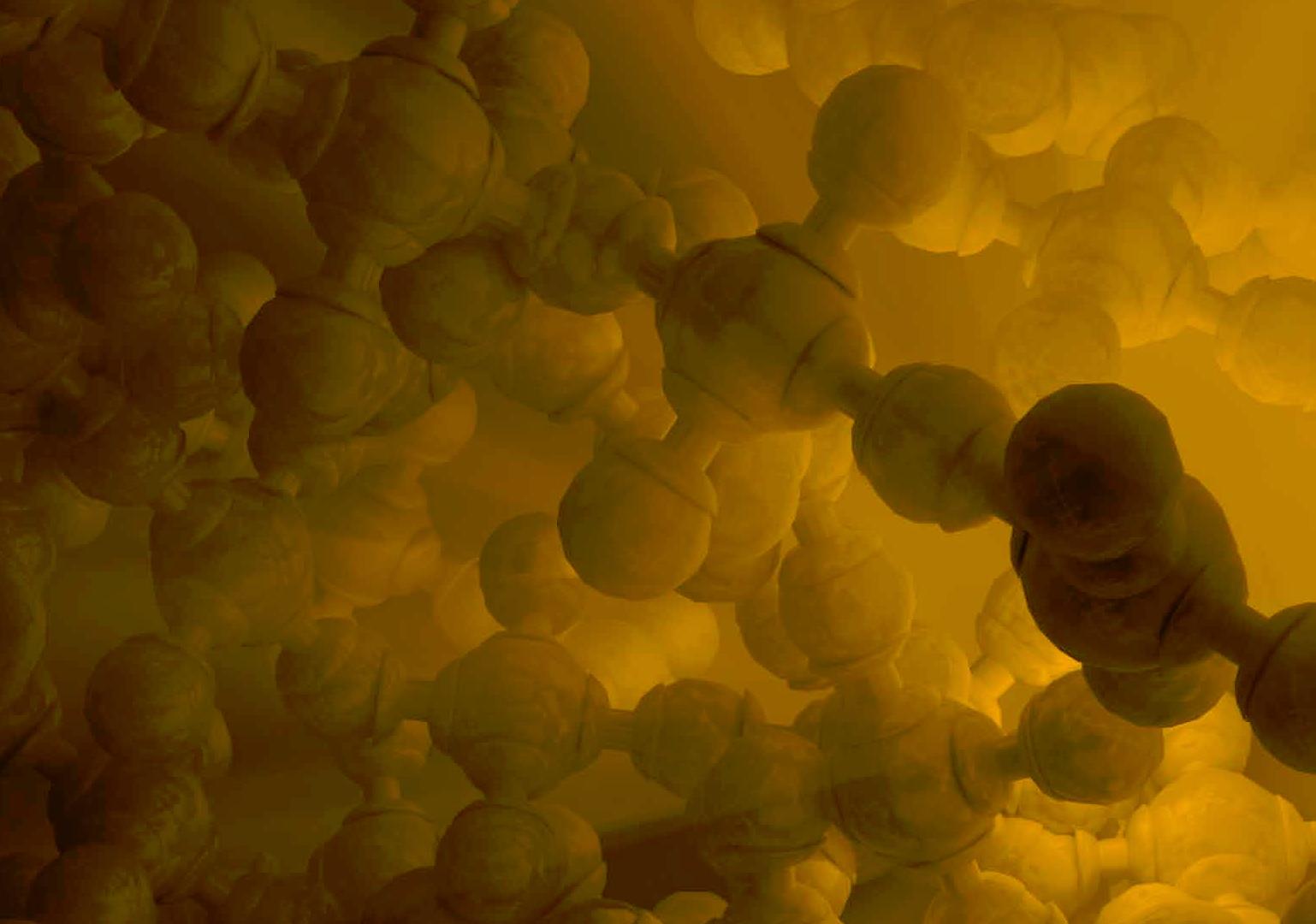
In the midst of South Africa’s emergence as a centre of oil and gas activity, the opening of One Eighty Engineering Solutions’ new materials testing centre will provide local specialised services.
The most developed economy in sub-Saharan Africa, South Africa’s long history of excellence in sectors such as mining, resource extraction and maritime services is well documented. The industry, however, that has been undergoing rapid development in more recent years is oil and gas, in particular the upstream market. Today the country plays host to a significant supplier base, a capacity that is complemented further by the presence of a number of the world’s leading service companies.
“It was ten years ago, in 2002, that I started up the company,” explains Janet Cotton, founder and director, “after recognising the industry’s need for metallurgical consultant work and materials testing capabilities.” In the decade since its formation the company has gone on to develop a client base of over 300 organisations and businesses. Delivering creative, high value engineering solutions in the form of key information, One Eighty has come to be recognised as a leader in materials and metallurgical expertise.
Today, One Eighty is undergoing something of a transition. Whereas in the past it would subcontract the testing work that was required as part of a consultation, a substantial investment and support from Allseas, a Swiss offshore contractor currently executing a pipe lay project for PetroSA, has provided it with the capital needed to construct a materials testing centre that will allow it to carry this out in-house.
Expected to be up and running by the end of the year, the testing centre, with its state-of-the-art equipment will place One Eighty in the unique position of having capabilities that are otherwise unavailable in Cape Town. “While some companies do offer some materials testing,” research, development and design engineer, Suzanne Higgins says, “only we will have the ability to carry out a full study for a customer with all the equipment required to do so.”
It is companies within the oil and gas sector that are showing an increasing interest in One Eighty’s materials testing capabilities, particularly as it relates to weld procedure qualifications. Before commencing work on a ship or a rig an operator has to ensure that they first qualify the weld procedure. This is done through a series of impact and hardness tests carried out to the necessary standards. “With oil and gas activity expanding across the region,” Cotton continues, “this service is becoming more in demand and we have identified it as one of our biggest growth markets going forward.”
Upon the opening of its materials testing facility, One Eighty will possess one of the very few laboratories in South Africa with the ability to offer weld procedure and performance qualification test. Any oil and gas related construction involving welds has to undergo these procedures and performance related tests before work can be commenced. The procedure tests relate to the type of welding and the performance tests refers to the welder or weld operator. At its new premises, the company will be able to conduct tensile, bend and impact tests, before providing its customers with a detailed report. These tests will not be limited to the oil and gas sector. Customers from various other industries will be able to make use of them.
In addition to materials testing, One Eighty provides comprehensive failure investigation and material selection services. “What also makes us unique,” states quality assurance manager, Petra Gress, “is that, as a company, One Eighty actively works to bring engineering and science together. By having experts in fields such as material science, mechanical engineering and chemistry under one roof we are able to approach each project from multiple angles.”
A recent example of the company’s materials testing capabilities being put to use involved the hull of a vessel failing whilst at sea and the subsequent tensile and burn testing of the hull material by One Eighty to determine the quality of the lay-up of the various components of the vessel. In addition to these tests a microstructural examination was conducted and it was this that identified that the crack that led to the failure of the vessel developed in the centre part of the laminate. It was further determined that this part of the laminate was indeed more prone to fracture than the outer layers as the volume fraction of fibres in this region is lower.
There are numerous other case studies that highlight One Eighty’s expertise in the fields of failure investigation and material selection. One of its undertakings in the former saw it responding to a customer’s concerns when two electric motors used for cutting hot glass experienced catastrophic failure. Estimated to have been in constant operation for three days prior to failure, in both cases the issue appeared to stem from a fracture adjacent to the bearing.
Evidence collected by One Eighty identified that the drive shaft failed as a result of fatigue cracking, due to rotating bending. This implies that the applied stress had exceeded the fatigue strength of the material at the site of fracture, with the loose fit between the shaft and the fan being the most likely cause for failure. Stress analysis calculations confirmed that the fan wobble was sufficient to cause fatigue fracture within the reported operating hours.
From a materials selection point of view, the analysis the company carried out on a hinge pin on a diving bell door also stands out. In this case the customer in question reported the pin showing severe galling over time, resulting in difficulty opening and closing the door. What One Eighty was able to recommend was that to reduce this galling, the surface finish, lubricant selection and material selection must be optimised. It also highlighted that using a lubricant containing a solid element would produce the best results, creating a barrier between surfaces and preventing the effects of cold welding.
It was through the company’s membership status within The South African Oil and Gas Alliance (SAOGA) that it was able to ascertain whether there was in fact a need for a materials testing facility in the Western Cape of the country. “The feedback we received from fellow members,” Cotton says, “was overwhelmingly positive, with the consensus being that, in order for the region to provide world-class services to large oil and gas players, a local test centre is essential.”
Despite being a fundamental aspect of manufacturing, metallurgical services remain highly specialised and as such are not widely available in South Africa. What One Eighty is able to do as a member of SAOGA is use its expertise and knowledge to educate people as to the importance of these services. The SAOGA can in turn distribute this to its members.
“As oil and gas activities increase in South Africa,” Cotton says, “it becomes all the more important to have the right degree of materials testing knowledge and experience available locally to service this growth.” Without access to local facilities, companies would otherwise be forced to continue sending work back to Europe. One Eighty’s facility will not only help eliminate the logistical and economic burden that comes from this, it will also provide the opportunity for customers to get a better understanding of the process and its results through closer, more direct interaction.
Over the course of the next two years, the company is committed to its aim of taking its materials testing facility from zero percent capacity to at least 75 percent capacity and beyond. “With the opening of the new centre,” Higgins enthuses, “comes a great number of new opportunities. We know there is lots of work out there and this gives us all a great deal of excitement for what the future holds.”
In the meantime, not only does One Eighty intend to expand its consultancy business internationally, its founder and director has her own personal goal that she wants to see come to fruition and that is for the company to branch out into product development. “This is something I am hoping to see became a much stronger theme for the business over the next five years,” Cotton concludes. “Whether it involves developing our own range of products or specific, bespoke items for a customer, I envision One Eighty’s business being balanced between consulting, materials testing and product development.”
Written by Will Daynes, research by James Boyle
DOWNLOAD
OneEighty-EMEA-Nov12-Bro-s_0.pdf