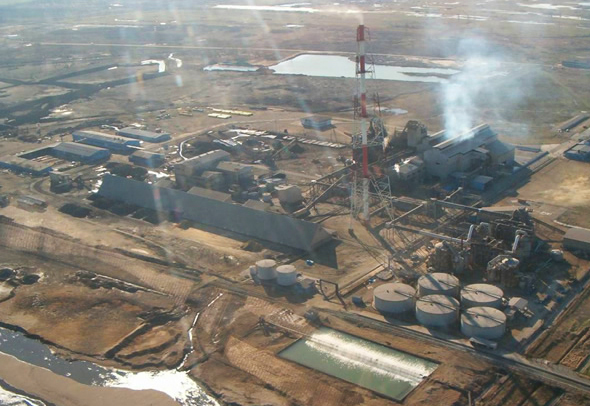
The Turkish economy grew in a highly protectionist mould for more than half a century following the foundation of the modern republic after World War 1. However, in 1983 Prime Minister Turgut Özal initiated a series of reforms designed to shift the economy toward a more private sector, market-based model and since then many former state-owned enterprises have been privatised. One of Turkey’s largest integrated mining and beneficiation company’s is Eti, which has a number of subsidiary units responsible for several mining activities throughout Turkey. As a result of the privatisation policy some of these activities have been sold to indigenous operators. One of these is Eti Bakir.
Bakir means copper in Turkish – this is a copper producing company, operating from a large facility is located on a three square kilometre site at Tekkeköy, 16 kilometres to the east of Samsun in northern Turkey, on the Black Sea coast. Construction of the Samsun plant started in May 1968, and in March 1973 it produced its first batch of blister copper – a 93-95 percent pure copper product. The plant has processed copper concentrates from mines all around the Black Sea region, but a large proportion comes from northern Turkey – Damar to the east and Küre to the west.
Eti Bakir was privatised in 2004 and, along with the smelter and acid factory in Samsun and the flotation plant that processes and enriches the slag from the flash furnace, sold to Cengiz Holding Company, an industrial group that started in 1980 with construction interests but has since diversified into aviation, tourism and energy as well as mining. When it took over Eti Bakir Cengiz started to acquire the major upstream facilities the plant depends on, taking over the mining company Küre Copper Corporation (KCC). Also in 2006, Murgul Copper Corporation (MCC) which was again a public corporation, was privatized and was taken over by Cengiz Holding In 2008, Cengiz went on to purchase the Izmir-Ödemi Antimony Mine when that was privatised, and all four corporations now operate under the name of Eti Bakir AS. Eti Bakir also owns the Uludag wolfram (tungsten) mine near Bursa, where feasibility work is still being carried out.
So Eti Bakir mines copper in two similar mining regions. The Küre Mine of Eti Bakir is located in the northwestern part of Turkey, near the city of Kastamonu, close to the Black Sea. The Murgul Mine is operated in the far northeast of Turkey, close to the town Murgul in the province of the city of Artvin. The Küre Mine includes three open-pit mines as well as one underground mine. It is located in an earthquake-prone region, so underground operations are a challenge, requiring the best available stabilisation equipment such as DSI's Omega-Bolt expandable friction bolts, which are flexible enough to withstand the changing conditions of the terrain as well as being able to link multiple weak strata layers reliably to secure this seismically active rock. These bolts are continuously installed in the shaft and galleries during tunnel driving. Additionally, last year the company achieved a national deep drilling record last year at this mine. It drilled to 1,870 metres using its own Boart Longyear LF230 rig.
At the time of privatisation KCC was already producing unsorted ore from open and underground mines and concentrating it; however in 2009 the reserves of open mines were running out though production at the nearby Asikoy underground mine and Bakibaba, where preparatory and investment work is still being carried out, is continuing. When the investment in Bakibaba Mine is completed in 2015, production which currently stands at 100,000 tonnes per annum (tpa) with 18 percent copper content will be increased to 140,000 tpa.
MCC is at present producing 120,000 tonnes of copper concentrate at 22 percent concentration from 3,500,000 tonnes of crude ore per year. In addition it operates a 35MW hydro-electricity power plant. Concentrate coming into the Samsun plant from these sources is stockpiled in 17 separate stockpiles each of 2,000 tonnes, giving an overall stockpile capacity of 50,000 tonnes. The concentrate is loaded onto conveyors that take it to the furnaces.
When the Samsun Smelter Plant was taken over from government ownership, it only had the capacity to produce 40,000 tpa of blister copper and 200,000 tonnes of sulphuric acid. After major investments by Cengiz which saw the addition of a new 70,000 tpa capacity anode and cathode plant and the modernisation of the acid production plant, the facility now has the ability to produce 250,000 tpa of sulphuric acid. The plant has three main elements, the drying furnace, the flash furnace and the converter.
Blister copper produced by Eti Bakir is so called because of its appearance. Smelting of ore with copper sulphide and iron sulphide minerals like the concentrates from Küre or Damar separates out the metal. The concentrate is fed into the rotary kiln-type drying furnace, which operates at over 300 degrees C, at a rate of 45 tonnes per hour: when supplied it has a moisture content of between nine and twelve percent and this needs to be reduced to around two percent improve production quality and the efficiency of the flash furnace into which the dried concentrate is then fed. The minerals are partially oxidized and melted, resulting in segregated layers. The matte layer refers to the iron-copper sulphide mixture which sinks to the bottom. The slag, which refers to the remaining impurities, floats on top of the matte.
The slag is sold on to be used in construction or as sandblasting grit, but it also contains recoverable amounts of copper so is first sent to a flotation plant. The sulphur dioxide gases are collected and converted to sulphuric acid. After a long refining process the converted copper, with its characteristic blisters left by the gas bubbles after the cooling process, is recovered ready for further refining.
Cengiz continues to invest in Eti Bakir, aiming to make it a world-class facility in every respect. The first half of this year will see the opening of a new plant on the Samsun site that will produce 250,000 of ammonium sulphate fertiliser. This will mop up some of the overproduction of sulphuric acid, and take advantage of a great opportunity to add value to this commodity.
Written by John O'Hanlon, research by Paul Bradley
DOWNLOAD
ETIBaker-Euro.Mining-Mar13-Bro-s.pdf