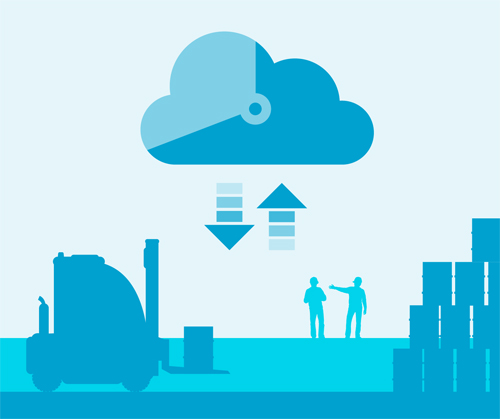
Rich Hite, President of QC Software, a Tier 1 warehouse control systems solutions provider, suggested, “Even the best WMS has a brief lag time in transmitting of instructions to a high-speed sortation system. There are simply too many warehouses with tens of thousands of decisions being made daily that require split-second timing.”
Hite, along with other industry leaders agree there is a place for both warehouse management systems (WMS) and warehouse control systems (WCS). Thomas N. Williams is a global expert on WMS and WCS solutions. His client roster includes Home Depot (Atlanta, GA), UPS Airhub (Louisville, KY), and Under Armour (Baltimore, MD). As a systems and industrial engineer with thirty-five years of experience, he has designed, developed, and implemented highly productive and cost-effective software and hardware solutions for high-volume distribution systems. His company has won national awards for design in both the US and Canada.
Williams noted, “The Material Handling industry continues to change. Recently, ecommerce and multichannel distribution have added new layers of complexity to the supply chain. The IT industry has evolved in response to these changes.”
James Cooke, Editor at Large for DC Velocity has covered logistics and transportation as well as supply chain strategy and technology for two decades. A former editor at Logistics Management magazine, he has earned numerous awards for his well-written, in-depth articles spotlighting developments in distribution. Cooke helped drive the launch of Supply Chain Management Review. He is a frequent speaker on the logistics conference circuit.
Cooke offered warnings about cloud-based WMS solutions suggesting, “When it comes to their software, a lot of warehouse and DC managers have their heads in the clouds these days. Rather than buying a traditional warehouse management system (WMS) and installing it on their corporate servers, they’re opting for cloud-based applications that are hosted by the vendor or a third-party on an off-site server, often far away, and delivered via the Internet.”
He also acknowledged, “Much of the appeal of cloud-based solutions is their low cost. Companies can avoid a hefty upfront capital outlay for software licenses as well as ongoing expenses for upgrades and maintenance. At present, most cloud-based WMS users are small warehouses that use basic equipment like forklift trucks, bar-code scanners, and radio-frequency devices in their operations.”
The WMS is the freighter moving slowly across the ocean (or more literally in a cloud-based transactional modality. The WCS is the agile solution that operates within the four walls of a plant or distribution center. WCS is the speed boat. There is value in both the WMS and WCS, yet as the high volume distribution centers with B2C (Business to Consumer) focus attempt to cope with exponential proliferation of SKUs, the WCS is keeping an important reality check.
Cooke consulted several industry experts who insisted, “To prevent these kinds of delays, a robust warehouse control system is essential.” Hite agreed that a WCS, installed at the warehouse, serves as a local agent for the remote WMS, downloading information on what items need to be put away or retrieved from inventory and then converting the information into instructions for the sorters, carousels, conveyors, carrying out the required tasks. Because the WCS processes data on-site, delays caused by communication disruptions are virtually eliminated.”
Often a WCS executes instructions provided by an upper-level host system, such as an enterprise resource planning (ERP) system or a WMS system. Tier-one WCS software provides advanced management capabilities including inventory control, resource scheduling and order management. The best-of-breed WCS systems are modular in nature, easily configurable and platform independent, with a scalable architecture to satisfy the needs of any size warehouse. There is confusion when to apply a WMS software solution versus a WCS which directs real-time data management and interface responsibilities of the material handling system as well as provides common user interface screens for monitoring, control, and diagnostics.
The focal point for managing the operational aspects of the material handling system, WCS provides the critical link between the batch-time data host and the real-time programmable logic controller (PLC) material-handling system. The PLC coordinates the various real-time control devices to accomplish the daily workload. At each decision point in the distribution process, the WCS “determines” the most efficient routing of the product and transmits directives to the equipment controllers to achieve the desired result. The decision-making process is often controlled by two separate utilities, the sort manager and the route director.
Cartonization allows picking directly to shipping container and eliminates movement from pick container to shipping carton. The size and number of cartons are projected up front and the shipping method and cost can be calculated up front as well. This aspect of a warehouse control system (WCS) is vital. Looking the available carton sizes defined by the customer or the carrier also allows for MHE considerations. Cartonization also allows for in-line weight tolerance checking. This is but one element of the WCS and is quite distinction from the purpose and functionality of a warehouse management system (WMS).
Wave Management controls release of work to the floor and is an important part of warehouse control systems (WCS) and differentiates warehouse management systems (WMS). Work flow can be managed via a wave or waveless operation; group picks are made by order attributes such as shipping method or delivery zone, order types, or pick zones. WCS allows warehouses to limit wave size to balance picking activity and balance picking by zone. There is also the ability to limit work by destination, if required.
Often the conversation of WCS versus WMS arises when other inefficiencies are located in the packaging operation, such as orders picked into a tote, not into shipping cartons. This presents a challenge because when the tote is sent to the packing area, the packing operator must select the correct box for the contents, pack it, seal it, and forward it to shipping. Most companies require a system that allows for multiple carriers, where the server passes information only once per day.
One of the schemes many WMS solutions providers utilize to drive increased revenue is to modify a WMS solution to resemble a WCS. Modification is code for charging more money. Once WMS modifications are made, upgrades need to be verified as compatible and integrated with other IT systems (including, but not limited to, ERP - enterprise resource planning software). Some WMS upgrades are a deliberate revenue generating plan for the technology vendor via verification processes and procedures. The cost of these modifications, verification checks and double-checks are often more expensive than the outright purchase of a Tier 1 WCS.
Warehouse control systems are not for everyone; yet as lean efficiencies are mandated many companies are looking at WCS solutions which enable them to streamline warehouse operations with a low total cost of ownership.