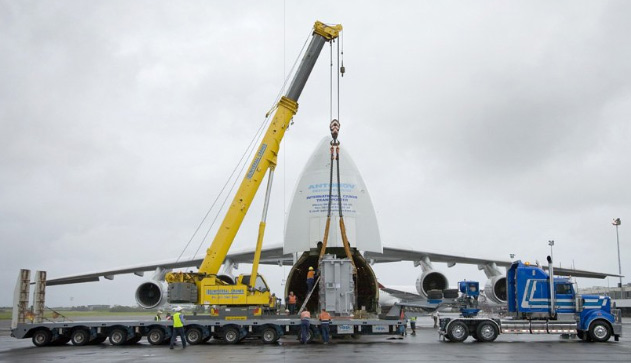
As 2009 drew to a close and most Queenslanders were enjoying the Christmas break, ABB Australia pulled off a remarkable feat of engineering collaboration, logistics and lateral planning. Its client, CS Energy, was rather impressed, as John O’Hanlon discovers.
When writing about ABB it is usually difficult to know where to start. The $30 billion power and automation group, with its Swiss origins, is as well known for its flat management and global communications as for its technology. And ABB Australia doesn’t make focusing any easier: with eye-catching contributions to the alternative energy, manufacturing and mining sectors as well as infrastructure of every description, ABB is nothing if not diverse.
However, one recent project really pulls together ABB Australia’s capacity to wrap up planning, design, manufacturing, logistic and commissioning capabilities in delivering an extraordinary result for its client. When Queensland’s main power supply company CS Energy needed a new transformer for its 750MW coal fired Kogan Creek generating plant, it not only needed a reliable solution for a unit; it needed it really quickly, to meet time-critical operational requirements. This was a business-critical order and time was of the essence.
ABB’s engineers quickly saw need for a design capable of meeting the challenging service conditions.They quickly came up with a robust solution, a purpose-built design to meet the needs of CS Energy. The client, aware that the normal lead time for a transformer of this size would normally be around eight months and extremely keen to get beyond the temporary measures it had to adopt to keep the plant running, took some convincing, says Julian Guild, ABB Australia’s sales manager for power transformers. “We talked to our transformer factory in Thailand and were able to get them to commit to three months ex-works, including design.”
That in itself was a remarkable commitment, and very attractive to CS Energy, but as Guild points out, you’d normally have to add another four weeks to the lead time to ship such a transformer weighing over 60 tonnes to Australia—and on top of that you’d still have to allow time to deliver it to the site and install and commission it. The thinking caps went back on as ABB and CS Energy tried to figure out togetherhow not to squander the manufacturing time gain on logistics.
They called on a specialist, Townley Group International (TGI) and between them came up with a plan to airfreight the transformer. That would potentially dwindle the delivery time to a couple of days, but there are not many aircraft that can carry a 60 tonne payload. However, TGI was able to arrange the charter of an Antonov An-225 strategic airlift aircraft. The fact that the only available slot was on Christmas Day was going to present some problems, but if it meant the transformer could be brought on stream before the end of the year, that would just have to be overcome.
Convinced, CS Energy supplied ABB with a letter of intent in mid-September 2009, on the basis of which the project swung into gear. There’s no such thing as an off-the-shelf transformer, says Guild, and every one the factory near Bangkok produces is tailored to the specification of the client. However, there were some unusual needs in this case, related to the unusual method of delivery. “A transformer is essentially a pressure vessel; during transport you remove the mineral oil from it and fill it with dry nitrogen,” explains Guild. “But with the changes in altitude and therefore pressure, nitrogen is seen as a hazard: if it got out it could suffocate the entire aircrew! Very unusually, we had to keep the transformer ‘open’, so we fitted it with a dehydrating ‘breather’ which takes the moisture out of any air that goes into the tank. As soon as the plane landed we applied a vacuum to the transformer and refilled it with a dry inert gas ready for the road transport leg.”
Working with Antonov engineers, the ABB design team fitted the transformer with anchor points aligned to the plane’s securing stations to ensure there was no chance of the load shifting in transit. The job required TGI to attend the loading in Thailand and supervise the road transport section up to the airport on Christmas Day: the aircraft touched down at 1500 hours on Boxing Day.
The logistics and risk management involved made this a unique and outstanding project, says Guild. “To get the transformer to the airport on time, it was necessary to design and manufacture the transformer in less than half the normal period. Then we had to test it in the factory, pack it and prepare it for transport to meet a plane that had been scheduled two months previously! Between us we were able to coordinate that down to the minute.”
After a six-hour road trip, the new transformer arrived at Kogan Creek and was installed during the holiday period—a critical operation, as Guild recalls: “Once it reached the site it had to be installed, something that normally takes a week or so; but we were able to do that in less than three days. We had three shifts working 24 hours a day between Christmas and New Year.” In the event, the handover took place towards midnight on New Year’s Eve—quite a tribute to the teams who redefined the term ‘unsociable hours’!
The transformer has been fully operational since early January 2010; and Kogan Creek power station site manager Ivan Mapp was more than happy with ABB’s ability to deliver on time and on schedule: “We chose to work with ABB due to the expedience in lead time and their reputation within the industry. ABB offered a delivery time that was unmatched by any other competitor and we knew that they had the expertise and resources to deliver on what was promised.” http://www.abbaustralia.com.au