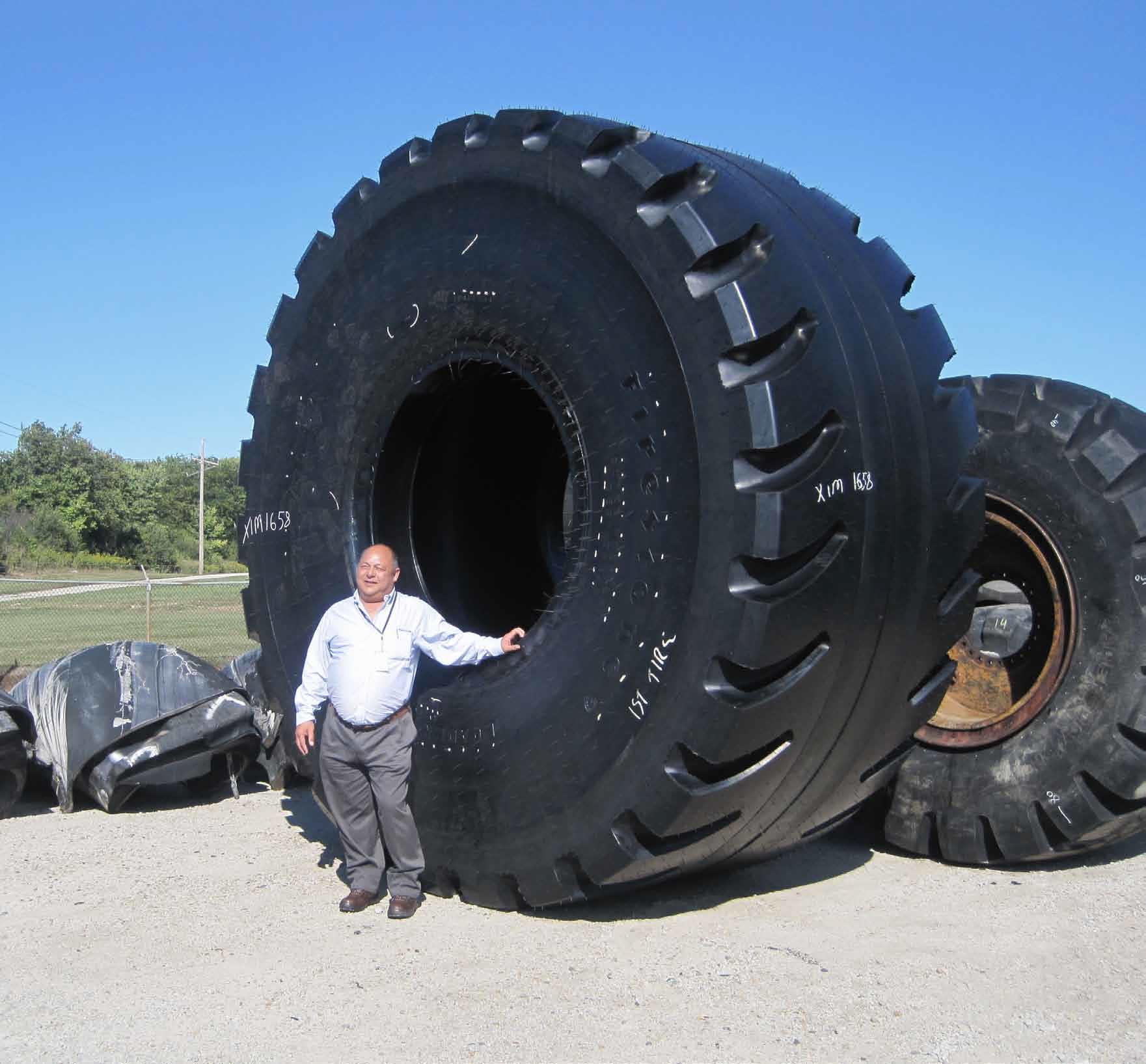
Bridgestone Corporation, headquartered in Tokyo, is the world’s largest tyre and rubber company; and its South African subsidiary is one of few able to supply and support the ultra large heavy-duty tyres suitable for underground and open pit mining.
South Africa is finally beginning to feel the effects of the global recession. When the banking crisis first hit, the South African economy was sheltered by its relatively low exposure to bad decisions in America and Europe and its own more robust financial sector. But the IMF’s World Economic Outlook Update of January 2012 IMF revised South Africa’s growth rate significantly lower for both 2012 and 2013. For 2012, the IMF’s growth forecast is now down at 2.5 per cent compared with an estimate of 3.6 per cent in September 2011; while for 2013 the growth rate was projected at 3.4 per cent, down from four per cent. The IMF suggested this was mainly due to the negative impact of the global economic slowdown.
The good news is that the country’s mining sector continues to expand and attract investment—it has slowed, but unlike construction it can’t grind to a halt in hard times: global demand for coal, manganese, iron ore, gold and all the other resources in which South Africa abounds remains and will increase.
Mining and construction are key sectors for Bridgestone South Africa. The latter is merely ticking over, says Jordon San, the multinational rubber and tyre manufacturer’s national operations manager, but his business is sustained by mining. There are changes in the market as the major mining companies add to their current fleets of trucks and excavators to meet their growing production demands; and one way or another, all these machines have to be shod.
The biggest headache is that there are not enough new tyres of the size and specification needed to keep these fleets going. This is an ongoing problem: the Bridgestone factories at Port Elizabeth and the Brits plant just outside Pretoria don’t manufacture anything bigger than 26.5 x 25 Firestone loader tyres, and they don’t have the capacity to make the large and ultra-large off road radial (ORR) tyres that are currently produced exclusively at Bridgestone Corporation’s Shimonoseki and Kitakyushu plants in Japan.
The shortage is forcing Bridgestone’s customers to face much more seriously the challenge to get the maximum life out of the tyres they have, and there is a lot that Bridgestone is trying to do to assist in increasing tyre life, says San. “Basically our job is to assist and advise the customer on how to use his tyres correctly under the right conditions, keep them at the correct pressure and train his operators in techniques that will extend the tyre life.” Simple measures like these can push the life of a tyre working under the most damaging conditions in an underground mine strewn with jagged rock particles by more than 10 per cent, representing a cost saving to the client and helping to overcome any delay in obtaining replacement tyres.
To put that in perspective, the average tyre life can gain a further 500 to 1,000 hours’ extra life, representing two or three months’ operation, simply by keeping the pressures and payload monitored and through sensible driving habits familiar to good on-road drivers—not accelerating or braking too fast, taking bends wider or more slowly. In a mine with a hundred or more heavy trucks, the cumulative saving is significant, and the same practices have a payoff in fuel efficiency as well, says San.
Bridgestone works with its clients to train operators in these techniques, and new technology is about to make it easier for them to get the best out of these giant tyres. A sophisticated tyre pressure and heat monitoring system called B-Tag is being manufactured in Japan and will soon be available to customers. A sensor in each tyre sends information to a control box in the cab, and is also connected to the mine’s monitoring system. If a tyre is showing signs of stress the truck can be called in for maintenance before actual damage or abnormal wear starts to happen.
However, there remains the problem of supply being outstripped by demand. Desperate to get replacements, some companies are prepared to pay silly prices on the ‘grey market’ for tyres sourced from other global markets but Bridgestone won’t support this type of price inflation, preferring to plan future needs with its clients and making every effort to keep the supply flowing. This has been made easier by recent expansions at the Japan factories and will further improve when a new $1.2 billion factory being built in America comes on stream in 2014.
The 1.5 million-square-foot off-road radial tire (ORR) manufacturing facility is being built on a greenfield site in Aiken County, South Carolina. “We won’t be importing any tyres direct from the States—the ones manufactured there will all be absorbed in the home market—but it will take a lot of pressure off Japan’s supply lines to the rest of the world,” says San. This is a major strategic investment by the global Bridgestone Group to enhance its supply systems, improve its sourcing flexibility and further strengthen the Bridgestone Group’s position as the global leader in the off-road radial tyre segment.
Another ORR plant being built in Thailand and scheduled to start production in 2015 will further improve global supply down the line, but a nearer term boost in supplies to South Africa is expected from a further $600 million expansion at Bridgestone’s Kitakyushu and Saga plants, for large and ultra-large ORR tyres for construction and mining vehicles and for steel cord used in these tyres respectively. This will enhance daily production at the Kitakyushu plant from 145 to 165 tons per day and will mean that Bridgestone can continue to supply the South African mining industry reliably through its current phase of retrenchment, and will be ready to pick up the baton once investment in fewer, larger machines kicks in. “We are expecting an upsurge in orders in the third quarter of 2012,” says San.
Written by John O’Hanlon; research by Robert Hodgson
DOWNLOAD
BridgestoneSA-EMEA-Sept12-Bro-s.pdf