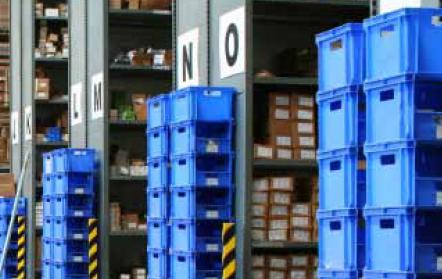
For many business leaders, managing the maintenance, repair & operations (MRO) supply chain has not always come top of the list of priorities. But to neglect it can cause major problems for a company’s ERP system in the long-term, leading to a number of knock-on effects that could easily have been avoided.
Most business enterprises typically put their energy, resources and investment into things like product design, sales & marketing, production efficiency, tight process control, information technology, and supply chain management both for inbound flows of direct materials and outbound flows of finished goods to end customers. With so many important priorities vying for attention, managing a company's maintenance, repair and operations (MRO) supply chain has typically been quite neglected.
In today’s economy, however, with much of the fat having been squeezed from direct materials supply chains, enterprises are taking a big interest in MRO. While MRO-related cost savings and process efficiencies are ripe for the picking, though, there is one huge problem: having never before controlled nor managed their MRO item and supplier masters in ERP, most companies’ source data is—to put it bluntly—a mess.
Consider, for a moment, the case of a manufacturing company that has neverhad a process in place to control when, how, or by whom materials item and supplier masters get created for MRO goods in ERP. Think about:
- The number of plants the company might be operating
- The geographic (and linguistic) sprawl of its plants
- The number of machines operating in the plants
- The number of moving parts within the machines
- The number of years in which the machines have been operating
- The number of different people who—over those years—have been called to service or repair the machines and purchase replacement parts for them
- The sheer quantity and variety of consumable MRO items that get used every day in operations
- The number of different suppliers that provide those consumable MRO items
- The number of mergers or acquisitions the company is likely to have gone through over the years
Very quickly, one gets a picture of the vast duplication, misclassification, inconsistency, and inaccuracy that permeates typical industrial enterprises’ ERP ecosystems related to MRO. And the MRO data problem sits at the root of a large host of challenges that stand between industrial companies and optimised MRO supply chains.
So what are the 10 epic fails in MRO master data management?
- Free-text MRO description: Unleashing people’s inner Shakespeare by letting each one choose their own words and writing styles to describe MRO items in ERP results in item descriptions that are cryptic, randomly and differently abbreviated, and often unintelligible to anyone other than the person who created them (and even to the person who created them if enough time passes). For example: is it a ball bearing, a brg, a ball brg, a bb, a b bear, a balbr, a bearing/ball type, a bearing (type unspecified)?
- Free-for-all ERP access: If anyone from the facilities manager to the storehouse operator is allowed to create new MRO item and supplier masters in ERP without providing protocols, policies or guidelines, then it results in massive duplication of records, causing big problems further down the road.
- Taxonomy-free MRO: Having no discernible taxonomy forces search and analysis activities into labour intensity and failure. Simple, high-level taxonomies may help somewhat with search, but leave detailed drilldown type analyses virtually impossible to accomplish without ad hoc manual or external classification exercises.
- No ownership: Giving people direct access to create item and supplier masters in ERP without a master data management (MDM) solution layer primed for data validation is just asking for incomplete, inconsistent and inaccurate data.
- No workflow for MRO: Workflow makes certain the right people pay attention and participate in the process. Most importantly, though, workflow makes it as easy as possible for a person to comply with policy.
- MRO safety stockpiles: Failure to find a part in inventory may lead to an unnecessary order, and it can also lead to unnecessary inventory. Safety stock might sit for years, dragging down MRO inventory turn rates and may still be sitting long after a machine has been taken out of service, causing obsolescence in MRO storerooms. Without any feasible ways to create clean, enterprise-level views of MRO stockpiles, inventory optimisation endeavours are doomed to fail.
- Preventive maintenance: While preventative maintenance is typically triggered by testing, visual inspection, electronic sensors and/or OEM recommendations for maintenance scheduling, insight into real parts consumption as it relates to particular machines might go a long way towards making preventative maintenance more science than art. Dirty MRO master data, however, makes such a scenario impossible to contemplate.
- MRO demand forecasting: Inability to accurately read MRO consumption patterns from an enterprise level undermines an organisation's ability to predict demand for consumable MRO items.
- Cash management & liquidity: Cash tied up in inventory or spent on non- or negative value adding work is not earning returns, hampering investment in innovation, capital expansion, future business development and growth. It also forces enterprises to finance more working capital for longer periods than necessary.
- Performance management: Systematic problems like poor MRO master data management can affect many people's job performance metrics negatively in ways that are not under their direct control. This corrupts the company's performance management system, leading to great personal frustration and low morale.
These failures thus provide us with a picture of the vast duplication, misclassification, inconsistency, and inaccuracy that permeates typical industrial enterprises’ ERP ecosystems related to MRO.
Zynapse is the Master Data Management (MDM) division of Zycus, the world’s leading provider ofspend management and master data management solutions to Global 1000 companies, which provides solutions for ERP projects and offers end-to-end automated ERP MDM solutions. The white paper 16 Epic Fails! In MRO Master Data Management, Plus the fastest way to fix them, discusses the pillars of MRO item management that help to manage a company’s MRO supply chain. http://www.zynapse.com/